What if excess material from production could be transformed into a valuable resource instead of waste? When our customer sought a solution for handling surplus wood from their sawing process, we set out to develop an intelligent robotic cell that sorts materials and enables their efficient reuse. The solution proved so effective that the investment pays for itself in just 2.5 years. Getting there, however, required engineering expertise, problem-solving skills, and a few unexpected insights.
Every production process generates some waste, but with automated sorting and smart material handling, this loss can be minimized. For businesses, this is not just an environmental concern, but a competitive advantage. Cost savings, resource optimization, and improved material efficiency all contribute to more profitable production.
In this project, the goal was more than just sorting. The robotic cell needed to enable the reuse of surplus material while integrating seamlessly into the customer’s production process. These are precisely the kinds of challenges where robotics provide practical, real-world solutions.
Achieving this required multidisciplinary expertise and close collaboration. Our team at Probot combined their skills to develop a solution that meets the customer’s needs efficiently and reliably.
Trust Built on Recommendations and Expertise
When the customer decided to invest in robotics, their collaboration with Probot began through strong industry recommendations:
– We were introduced to Probot through our contacts in the wood industry. The recommendations were so convincing that we decided to move forward with them, the customer explains.
While adopting new technology always comes with uncertainties, Probot’s experience in delivering customized solutions made the decision easier.
– There isn’t another factory like ours anywhere in the world. What helped our decision was that the system was designed entirely to fit our needs from the start. We wanted a solution that wouldn’t require major modifications later but would work as intended right away. That gave us confidence in our investment, the customer summarizes.
“In a country like Finland, where wages rise every year – not to mention global competition – companies must constantly develop and improve efficiency to stay ahead.”
– Customer
A Team at the Heart of Problem-Solving
A team of Probot experts took on this project, each bringing their specialized skills to the table. Project Coordinator Juha Polvela kept everything on track, while Aleksi Tyni and Eetu Koskela led the mechanical design. On the automation side, Eemeli Mutanen and Toni Autio tackled technical challenges. Eemeli also handled PLC programming and electrical design, while Toni was responsible for both automation design and robot coding. During the assembly phase, Jani Juntikka supported the installation work.
The project required extensive planning, from initial concept development to detailed design, testing, installation, and commissioning. In total, the project spanned approximately 10 months, kicking off on Valentine’s Day 2024.
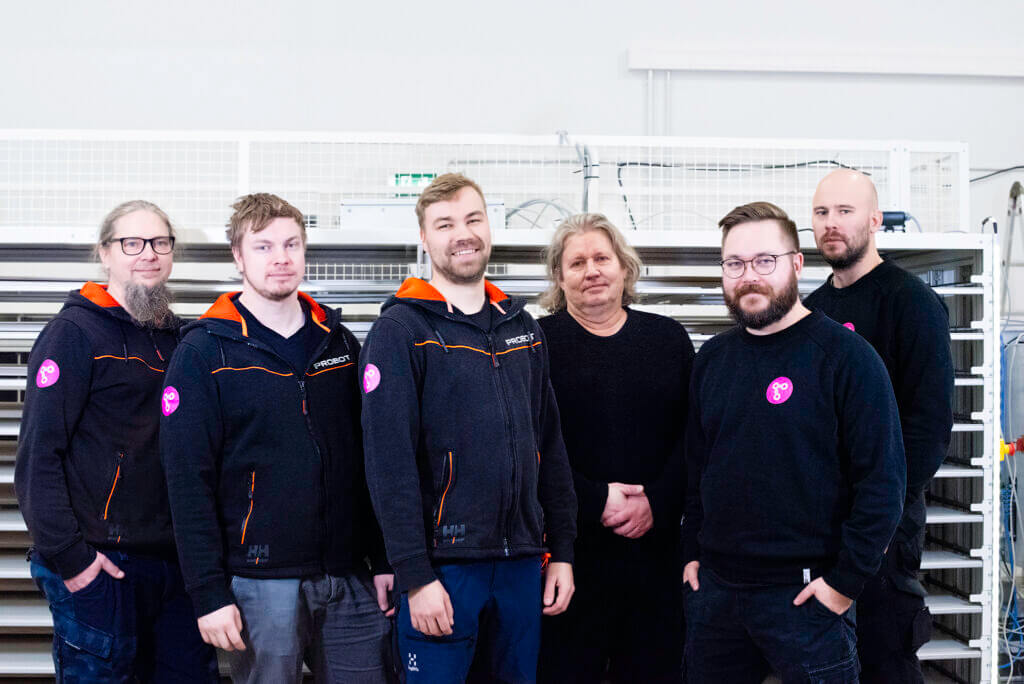
How the Robot Cell Works
In this solution, the robot cell operates as follows: the operator places the products on a tray and loads them into the cell.
– The robot picks up a piece, moves it for analysis, inspects its color, and measures groove depth and curvature, Aleksi explains.
– Once the vision system determines the product category, the robot places it in the correct sorting location. If the piece does not meet the criteria, it is sent to the reject pile.
One key detail is that the customer can utilize plywood sheets they already use in their production. The sorted products are placed on these sheets on designated shelves according to their category.
Sounds simple, right? In reality, designing this solution required overcoming multiple technical challenges. Next, we take a closer look at the biggest hurdles of the project and how they were tackled.
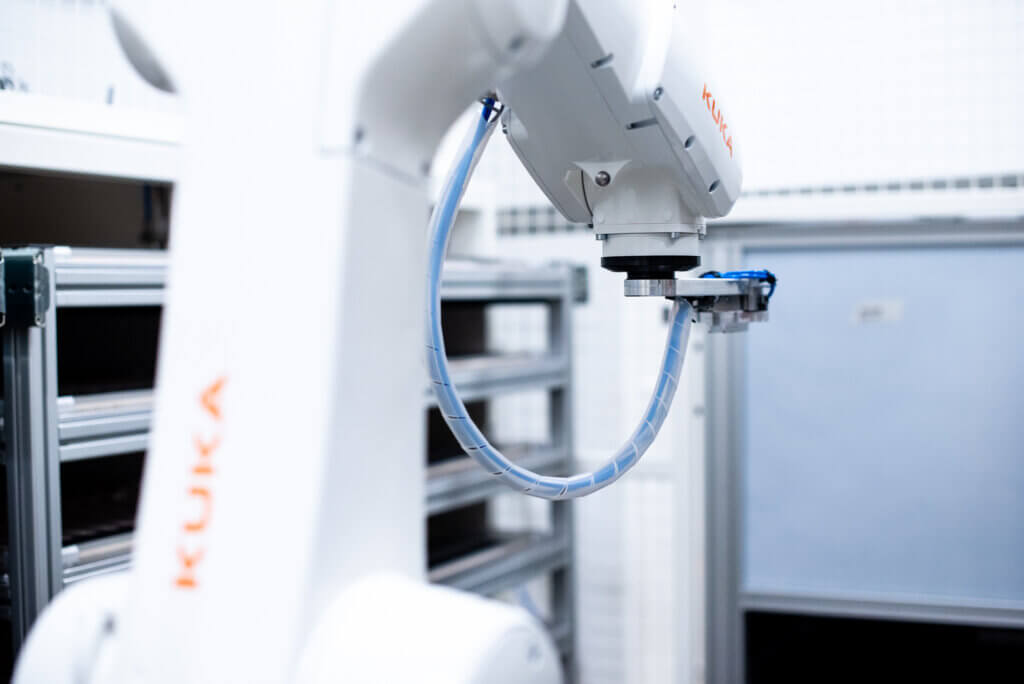
Customer Requirements Challenged the Design
While the robot cell is visually impressive, the real challenge lay in designing the automation and the entire system. The team had to consider the customer’s varying materials, production pace, and safety solutions. This project once again highlighted that developing a functional automation solution requires much more than just a robot and a gripper.
The customer had a clear vision of what they wanted the cell to achieve, but some requirements evolved during the project. The design process was guided by the following key constraints:
➡ The available space set the maximum size of the cell, which had to be considered from the start.
➡ The takt time was set at four pieces per minute.
➡ Products needed to be added and removed while the system was running, creating additional challenges for safety solutions.
➡ The number of product categories was high, requiring the cell to reliably identify and sort each piece.
➡ The feeding mechanism had to allow 400 products to be loaded at once.
➡ The nature of the material posed challenges, especially in the feeding phase. Wood is a demanding material as it reacts to humidity, and this effect is even more pronounced in thin, shaped pieces.
➡ The customer’s products were unique in shape, meaning there was no off-the-shelf solution for handling them. The cell required a fully customized design to ensure smooth and reliable processing.
Safety and usability went hand in hand in this project.
– Since products needed to be added and removed from the cell on the fly, we had to ensure safety without slowing down production, Aleksi explains.
“From the customer’s perspective, the most important thing is that the solution works. And it does.”
– Aleksi
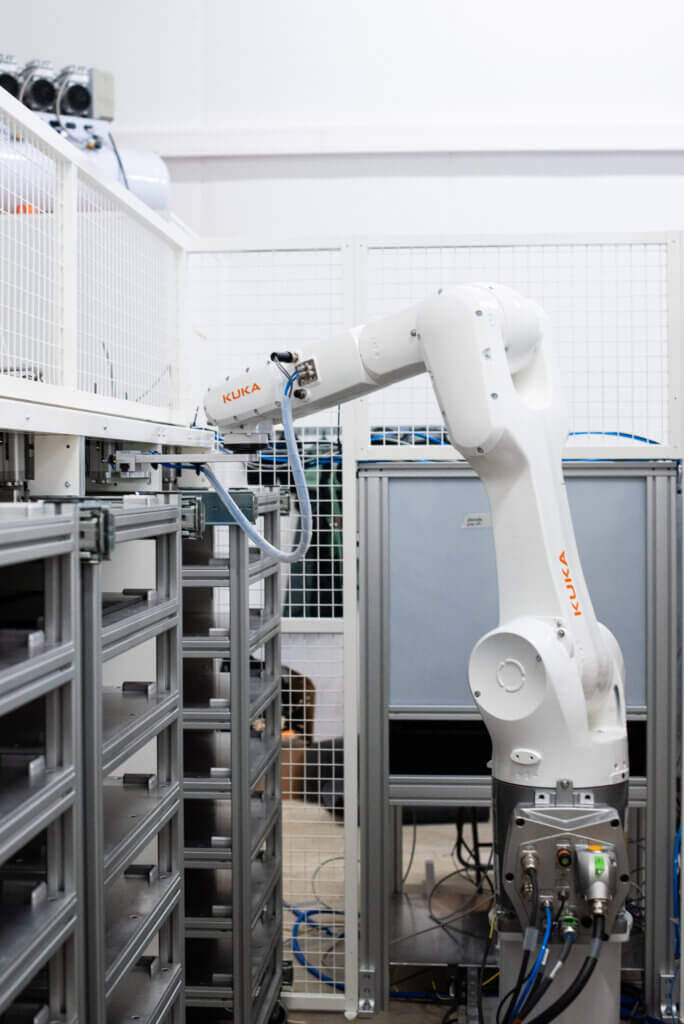
Technical Challenges on the Path to a Functional Solution
In this project, two key technical challenges stood out:
1. Precision Feeding for Machine Vision
Machine vision cannot simply “look” at objects. It must interpret their complexity. In this cell, machine vision identified key properties of each piece to determine the appropriate sorting category. However, this was no easy task, as the customer’s uniquely shaped products varied significantly. No two leftover pieces were identical, so sorting had to be based on multiple factors, including color, groove depth, and curvature.
– We had to ensure that every piece was positioned correctly for analysis. The challenge wasn’t just picking up the pieces but ensuring they were presented to the vision system in a way that enabled reliable measurement of color, groove depth, and curvature, Eetu explains.
The robot couldn’t just pick up pieces randomly. It had to grip them at the correct location and handle them reliably. The challenge wasn’t so much the gripping itself but rather ensuring that the varying pieces were consistently positioned in the exact same location and orientation for every pick.
2. Optimizing the Feeding Mechanism and Adapting to Production Pace
The feeding mechanism was another major development area, as handling the material proved more difficult than anticipated. The idea that the first design will work perfectly is a myth.
– The initial solution didn’t hold the pieces in the required position, so we had to modify the feeding process several times. Developing automation means being willing to experiment, discard, and improve solutions, Eemeli reminds.
Additionally, the solution had to adapt to the production line’s pace without slowing down the process.
Virtual Commissioning Saved Time
One of the biggest advantages of this project was the use of virtual commissioning, allowing us to run the robot at the customer’s site immediately after installation.
We created a realistic model of the robot cell in the KUKA Sim environment. The robot was programmed in the simulation, and software code was tested virtually before physical commissioning. This ensured synchronization between the PLC code and the robot program before installation, reducing errors. Software bugs were also caught before delivery, making the on-site startup process much smoother.
– Virtual commissioning was a huge advantage in this project. We were able to test and verify everything in advance, so there were no surprises on-site, Toni says.
“Automation can be implemented step by step, starting with individual bottlenecks.”
– Aleksi
Seamless Collaboration with the Customer
The installation of the robot cell took 3–4 days, and commissioning was completed in about a week. A smooth deployment was ensured by a well-prepared FAT (Factory Acceptance Test), which verified the system’s functionality before delivery. Additionally, a clear installation and commissioning plan, combined with seamless cooperation with the customer, helped accelerate the process.
– The installation went incredibly smoothly. The space was ready, and we received support from the customer whenever needed. A well-thought-out plan ensured everything went perfectly. It was a pleasure working with the customer, Aleksi says.
Close communication and clear documentation ensured that the solution precisely met the customer’s needs. The customer had such strong confidence in the implementation that the project progressed smoothly even without continuous oversight.
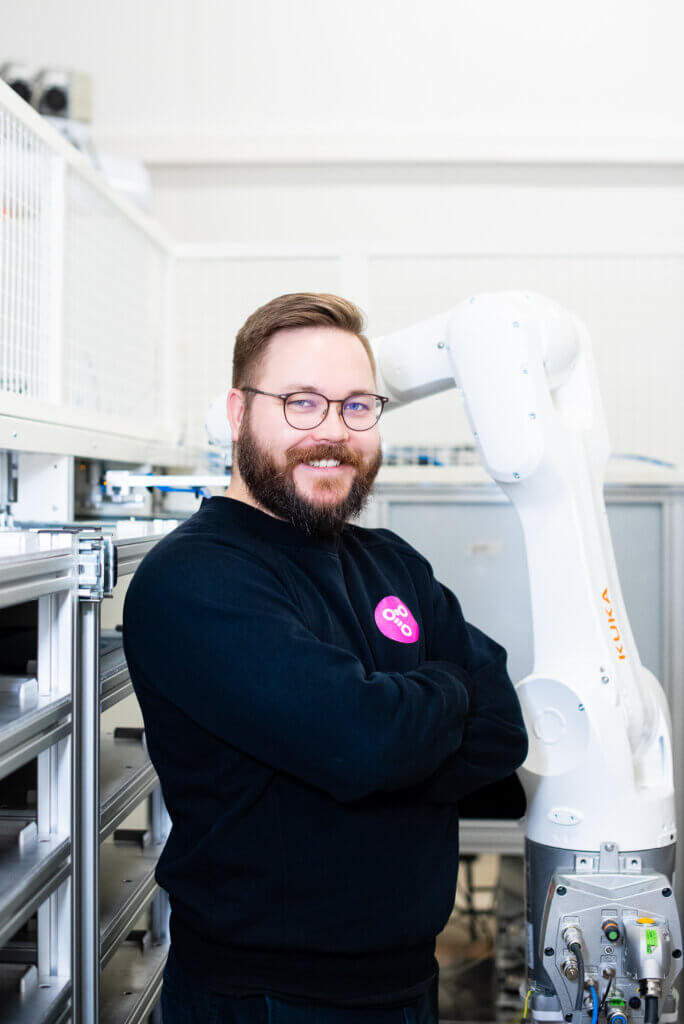
Workers Found a Teammate in the Robot
One of the biggest challenges in automation projects is often how employees react to new technology. Uncertainty and resistance to change are natural responses when a robot is introduced into a familiar work environment. This project was no exception, but perceptions changed quickly once employees saw the robot cell in action.
Initial concerns faded as staff realized the robot was there to enhance and support their work, not replace them. Management was particularly pleased with how seamlessly the new system integrated into daily operations.
– At first, there were rumors that the robot would replace employees. But once they saw it in operation, they understood its purpose. This doesn’t take away jobs. It helps us do our work better, the customer explains.
Why Is Now the Time for Automation?
For companies without prior experience in robotics and automation, taking the first step can seem daunting. However, this project demonstrated that automation doesn’t have to be an all-or-nothing transition. It can be implemented gradually in a way that aligns with business needs.
– This isn’t a mega-factory. This is just smart, practical business, our customer emphasizes, encouraging other mid-sized companies to consider automation.
– I believe many medium-sized production facilities in Finland could benefit from this. It just takes the courage to take that first step.
For this customer, investing in automation was a strategically important decision:
– In countries like Finland, where wages rise every year – not to mention global competition -companies need to constantly develop and improve efficiency to stay competitive.
When evaluating an investment, return on investment (ROI) is often a key factor:
– Right now, we estimate the payback period to be 2.5 years, which is already excellent. And once we fully utilize the system, it could be even shorter.
– Your first robot cell doesn’t have to be massive. The most important thing is to find a solution that genuinely serves production and makes daily work easier, Aleksi points out.
“Automation can significantly improve worker safety and ergonomics. It allows employees to shift to more meaningful tasks instead of monotonous, hazardous, or physically demanding work.”
– Aleksi
The Three Biggest Benefits of Automation:
1. Maintaining Competitiveness in Finland
Automation enables cost-efficient production domestically, helping to keep jobs in Finland.
– Robotics and automation undoubtedly enhance the competitiveness of Finnish companies, Eetu reflects.
2. Improving Job Satisfaction, Safety, and Ergonomics
When discussing robotics and automation, it’s important to look beyond just production efficiency.
– Automation can significantly improve worker safety and ergonomics. It frees employees from monotonous, hazardous, or physically demanding tasks, allowing them to focus on more meaningful work, Aleksi emphasizes.
The purpose of a robot is not to replace people or take away jobs.
– In this project, the robot didn’t eliminate any jobs – on the contrary, it created more. Previously, the customer’s surplus material went to waste, but now it is being put to good use, Eemeli points out.
3. A Gradual Transition to Automation Without a Massive Investment
Aleksi reminds us that automation can be introduced step by step, starting with specific bottlenecks in production.
– It’s completely understandable that automation might seem like a big leap. But it’s important to realize that it doesn’t mean changing the entire production process at once. We can work together to determine the smartest first step for your business, Eemeli adds.
– After this project, the customer now sees automation as a viable option, and it looks like they’re already considering their next automation investments, Toni shares.
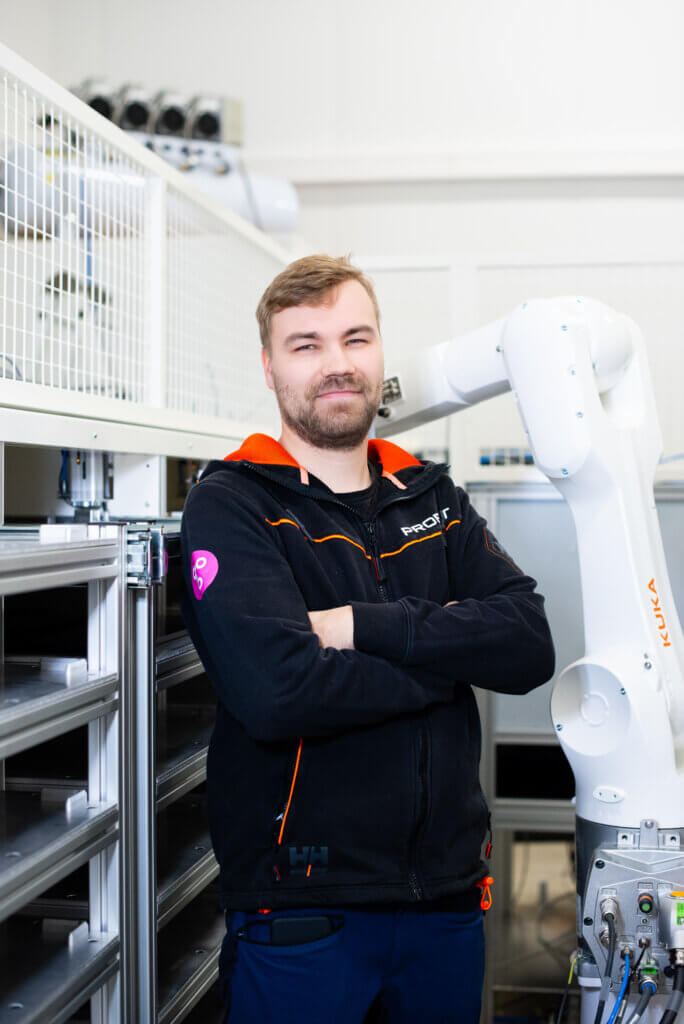
A Multifaceted Project and a Satisfied Customer
A successful automation solution is a carefully designed system where every detail supports the whole. The customer was highly satisfied with the solution we provided and the overall execution of the project.
– From the customer’s perspective, the most important thing is that the solution works. And it does, Aleksi sums up the project’s outcome.
For our team, the project was diverse and educational. It involved everything from mechanical design and programming to assembly and testing.
– We got to work on so many different aspects, from design and programming to installation. The team was fantastic, and working with the customer was smooth, the entire project team reflects.
A Unique Solution with Broad Application Possibilities
This robotic cell is the only one of its kind in the world. It was specifically designed for sorting and handling wooden materials, but its principles can be applied across various industries.
– By modifying the system, it can be tailored for sorting almost any type of product, Eetu explains.
Whether the challenge is minimizing waste, improving quality control, or optimizing production, the key to success lies in a deep understanding of both technology and the customer’s processes. This ensures that automation delivers real value – not just in terms of technology but also from a business perspective.
Want to learn more about how automation can optimize your production? Get in touch, and let’s design the perfect solution for your needs together.
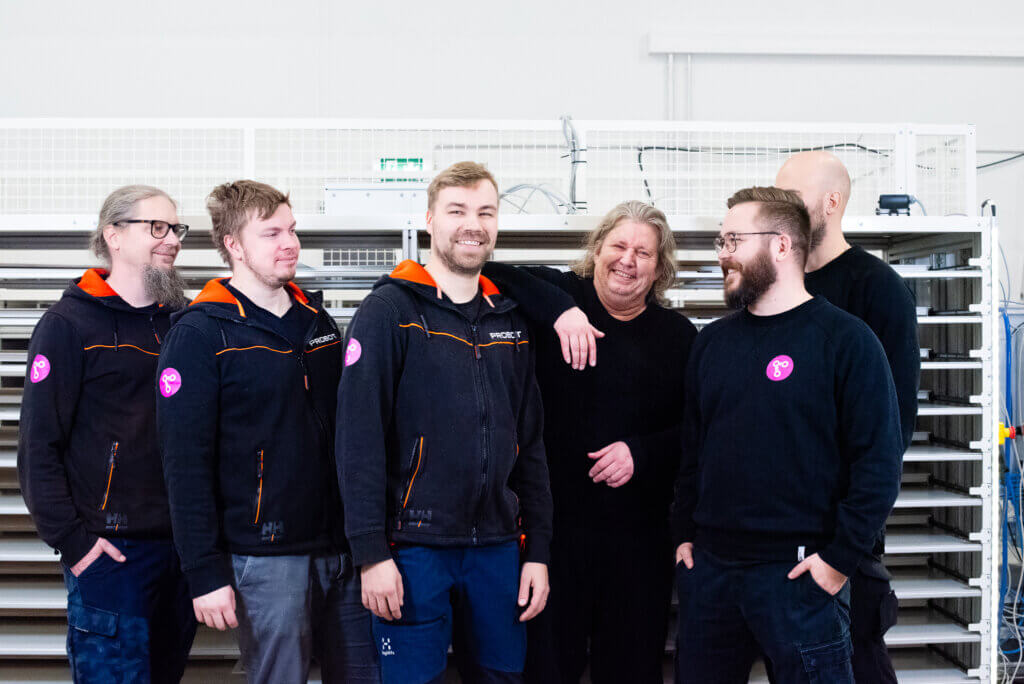
Read More:
- Explore the full project details in our reference case here.
- Interested in RFID technology or smart handling of small products? Read our blog post on RFID-based solutions here.
Probot Oy – Specialist in Robotics.