When our client sought a solution that minimizes waste in their production, a custom-designed robotic cell proved to be both an efficient and cost-effective investment. With a payback period of just 2.5 years and a significant reduction in material waste, this project is a great example of how automation can deliver tangible benefits – fast.
We designed and implemented an easy-to-use and highly efficient robotic solution that combines advanced machine vision with carefully engineered mechanical systems to sort and reuse excess material generated during the sawing process.
– Once we fully optimize the use of this system, the payback period might be even shorter than estimated, the client notes.
Our team meticulously planned every detail to ensure the solution operates seamlessly and safely within the client’s production environment and fits within the available space. Because no two production facilities are alike, the robotic cell was designed from the ground up to meet the client’s specific needs.
– We wanted a solution that wouldn’t require major modifications afterward but would work as intended from day one. That gave us confidence in our investment, the client explains.
Careful planning and execution made a lasting impression:
– The collaboration worked well, and the system works. When those two things are in place, everything else follows.
This robotic cell has proven to be a key investment in the client’s competitiveness. It not only minimizes waste and optimizes the current production but also lays the foundation for future development projects.
Efficient Material Handling with Machine Vision
The robotic cell is equipped with an advanced machine vision system that analyzes the color, groove depth, and curvature of each piece. The process begins when the operator places a tray on the system’s feed rack. Once the rack is confirmed and locked in place, the robot starts its work. Empty racks can also be refilled and activated while the system is running.
The robot picks up pieces one by one from the tray and transfers them to the inspection chamber, where a precise analysis is conducted. Inside the chamber, cylinders straighten and align the pieces to ensure highly accurate measurements. The machine vision system then identifies and classifies each piece based on predefined criteria.
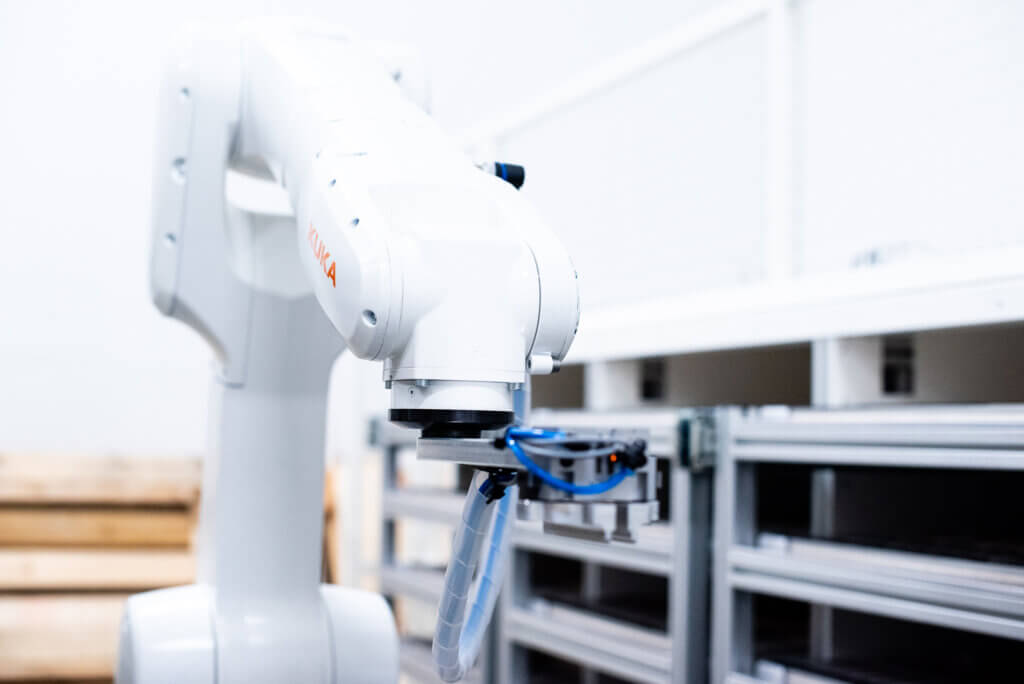
Smart Sorting and Quality Control
The machine vision system performs a multi-stage analysis for each piece:
- First, the system analyzes the color, sorting each piece into one of four color categories. Each category has its own specific criteria and tolerances for groove depth and curvature.
- Groove depth is measured precisely to ensure it meets the quality requirements of the assigned color category.
- Curvature is analyzed to separate usable pieces from those that must be rejected.
If a piece meets all the defined criteria, it is automatically sent forward for reuse. If any property falls outside the specified limits, the piece is rejected. However, rejected pieces can be reprocessed by placing them back on the tray and running them through the system again.
Once the piece’s properties have been determined, the robot places it in the correct category on a designated shelf in the output area. Each of the 24 categories has its own allocated space, and the operator can monitor the fill level in real time. When a shelf reaches capacity, the system notifies the operator that the pieces are ready for collection.
The system is designed to be flexible and seamlessly integrate into the customer’s existing processes. Piece loading and removal can also be done while the system is running.
User-Friendly Operation and Reliable Performance
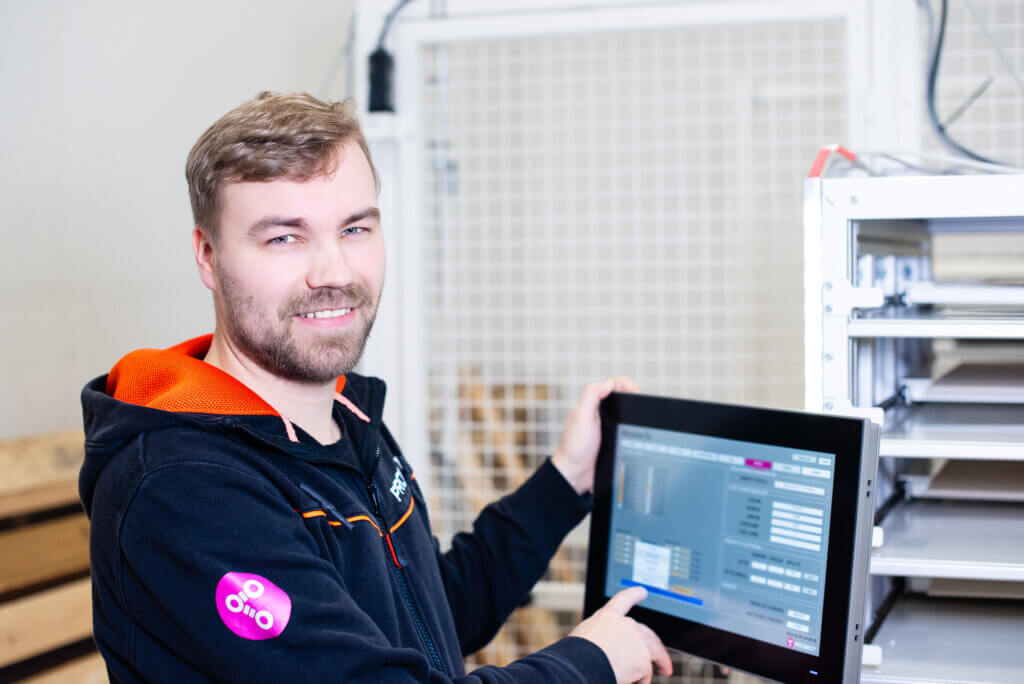
The ease of use of the robotic cell has been ensured through careful design. A clear user interface provides an instant overview of the process, guiding the operator step by step.
The mechanical solutions developed by our team ensure smooth material flow and safe operation. Maintenance and upgradeability have also been taken into account, making this solution a reliable long-term investment.
How Our Solution Supports Seamless Operation?
- Intuitive user interface and automated reporting
- Smooth integration into existing production processes
- Reliable, safe, and easy to maintain
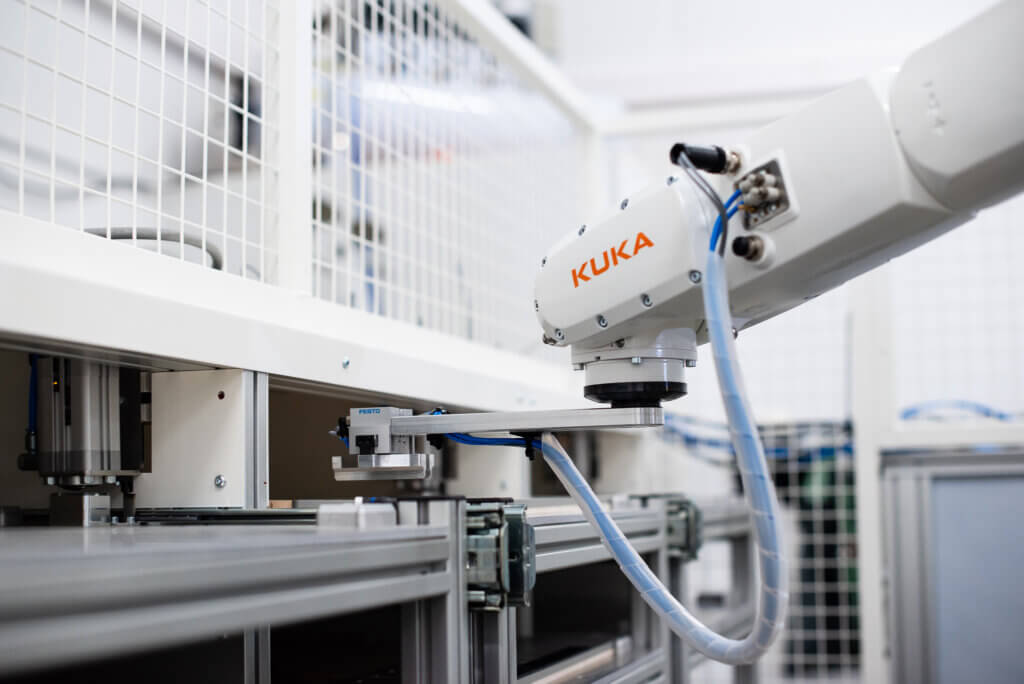
Versatile Applications
The robotic cell offers an efficient solution for material management and waste minimization. Automated measurement ensures precise quality control without the need for manual work. While the system operates autonomously, the operator plays a key role in monitoring the process and managing the input and output of materials.
This robotic cell is globally unique, but its technology can be tailored for various applications and requirements:
- Adaptable to different materials and part sizes
- Sorting criteria can be adjusted as needed
- Vision system can be customized to match specific requirements
- Scalable to accommodate varying production volumes
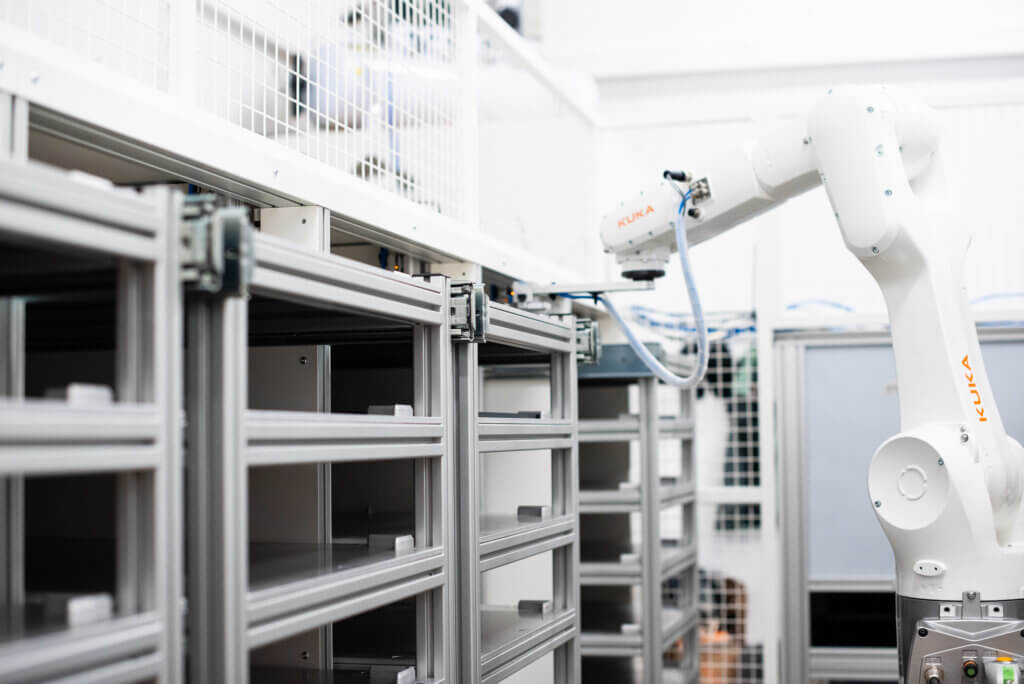
Key Benefits
- Minimizes waste – significant reduction of production waste
- Lower raw material costs
- Reduced environmental impact
- Automated quality control
- Efficient material handling and streamlined production
- User-friendly operation and management
A reliable partner in automation solutions
This robotic cell is a prime example of how our extensive experience in automation solutions is reflected in every detail, from installation to commissioning. In this project, virtual commissioning ensured that the system was tested and fully operational before installation, further accelerating the implementation process. A well-functioning automation solution is much more than just a robot – it’s a complete system where every component supports the others.
Seamless collaboration with the customer played a key role in this project. Clear communication and thorough documentation ensured that the solution met the customer’s exact needs. The customer had strong confidence in our team and felt that the project progressed smoothly without the need of constant oversight.
Whether it’s your first or tenth robotic cell, our team of experts ensures that the solution integrates seamlessly into your production and delivers immediate business benefits.
“The robot is impressive and works exactly as intended. I believe it’s a valuable investment.”
– Customer
Let’s talk automation! Get in touch with us here, and let’s build a solution tailored just for you!
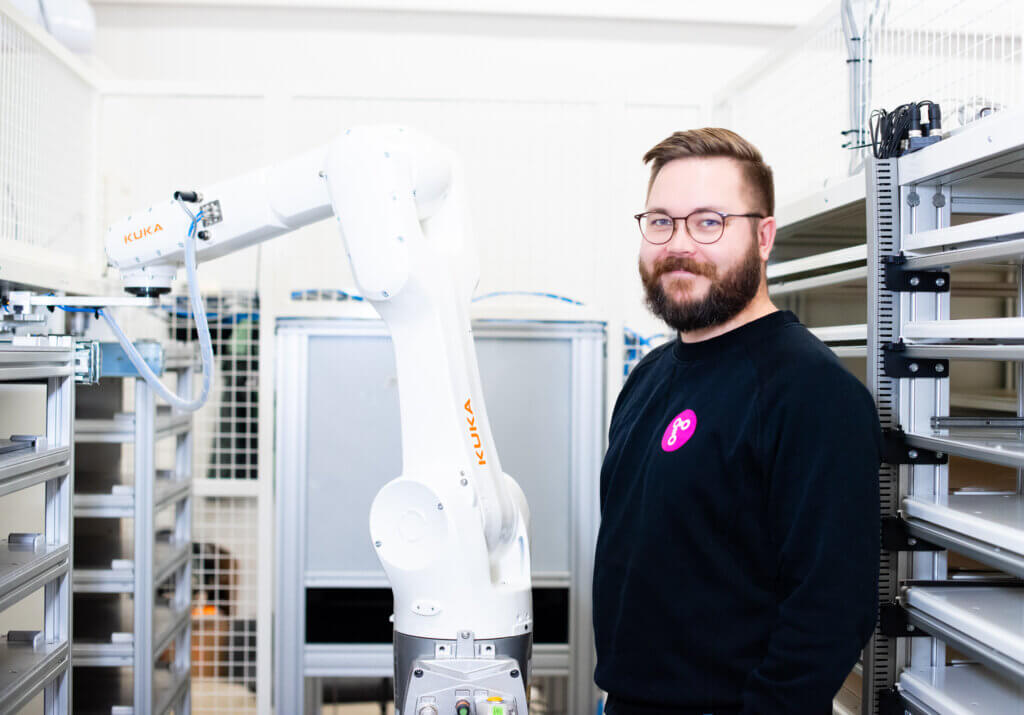
Interested in this smart sorting solution that minimizes waste? Check out our expert blog here and learn more about the project and how a robotic cell enhances efficiency in material handling.