Robotics and automation open up entirely new possibilities for improving production efficiency, reliability, and flexibility. When our client needed a modern solution for handling RFID tags, the Probot team took on the challenge. The result was a compact and customizable robotic cell, ideal for handling various small products. In this blog, we’ll share the surprises we encountered along the way, where we succeeded, and what we learned. Be sure to check out the video where we demonstrate the robotic cell in action!
The Probot team spent about a year working on an interesting robotic cell project when one of our client’s production cells needed an upgrade for the current decade. The client required a simple yet efficient system for handling RFID tags.
The Journey Towards a More Modern Production
The project progressed smoothly from the initial contact to implementation. Probot’s diverse team of experts took on the challenge, with key roles played by Project Coordinator Juha Polvela, Production Engineer Janne Paaso, Robotics Engineer Ville Iivari, and Automation Engineer Toni Autio.
Juha was responsible for sales, concept development, and overall project coordination. Janne designed the mechanical aspects of the robotic cell and assembled it. Ville managed the PLC software that controls the entire cell, while Toni handled the design and programming of the robot’s software. Ville and Toni also took care of the robotic cell’s testing and user training.
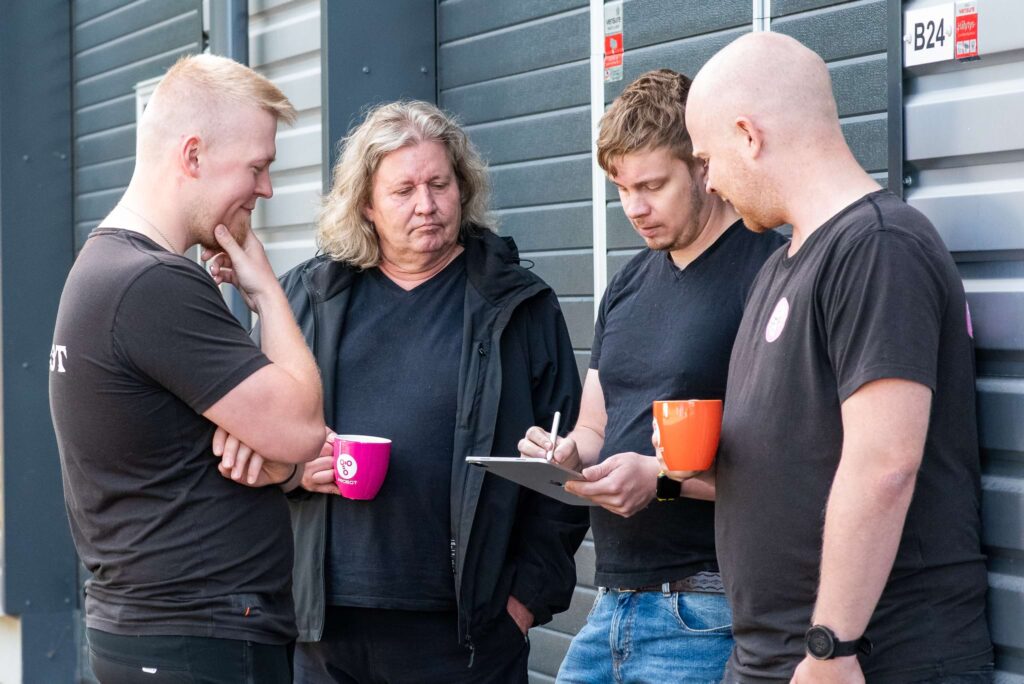
The component handling cell, completed in the summer, includes lift silos for feeding RFID tags, a SCARA robot for tag handling, and systems for tag programming, testing, and laser marking. The cell also features an intelligent product packaging system.
Juha’s 25 years of experience with RFID technology was extremely valuable to the project.
– RFID stands for Radio Frequency Identification. It is a remote identification technology that uses radio waves to transfer data. In designing the cell, it was crucial to ensure that interference from materials like metal was removed or isolated from the communication between the reader and the tags. Additionally, we carefully optimized the programming and testing distances for the tags, Juha explains.
“The client has been extremely satisfied with the outcome and has given positive feedback on the team’s professionalism, approach, and positive attitude. The project progressed according to plan, and the client felt that their needs were considered at every stage.”
Aiming for More Flexible and Efficient Production
The goal of the project was to create a durable and efficient device that operates reliably in all conditions. We wanted to modernize the equipment and enhance its performance. Special attention was given to improving production speed, automation, safety, and user-friendliness.
– Our client previously used an old, pneumatic-based device for handling RFID tags, but it was not reliable. The new robotic cell simplified and modernized the process, significantly improving reliability and reducing the need for constant supervision, Janne explains.
– The robot now handles most of the tasks, which speeds up and refines the handling of components. This boosts production, accelerates processes, and reduces errors, Toni summarizes.
– In addition, the intelligent order-number-based packaging system allows for the automatic, sequential processing of multiple orders. The user can queue orders, and the robotic cell efficiently packages them in order. This was not possible with the old machine, Ville adds.
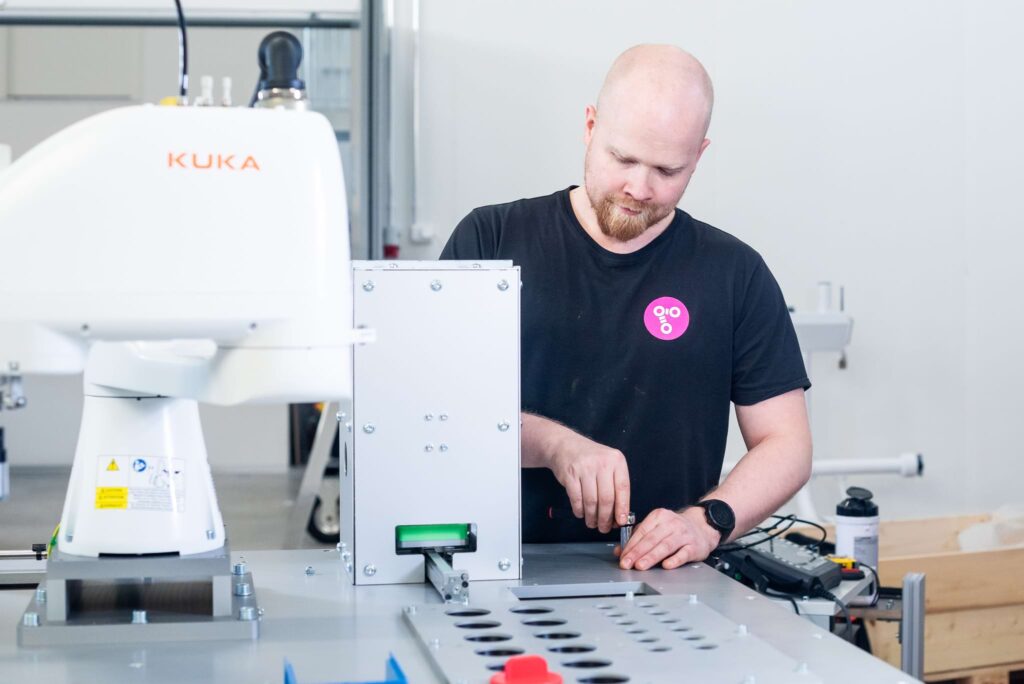
We utilized advanced technologies in the project, such as robotics programming, motor control, linear motion management, laser calibration, and RFID technology. Communication between the various systems, using protocols like TCP/IP and EtherCAT, played a crucial role.
– We are proficient in multiple communication protocols and ensured seamless integration between systems, Ville confirms.
– We also focused on customized mechanical design and safety with a dedicated safety logic. The user interface was made user-friendly and intuitive, Janne adds.
Overcoming Challenges Through Collaboration
As with any project, this one also faced challenges. The original timeline was about a year, but it was slightly extended due to unexpected product variations. The design process became more complex as the robotic cell needed to handle a wider range of product variants.
– Additional product variations came up unexpectedly, requiring us to redesign some aspects. We also encountered practical surprises, such as the static electricity and quality variations of RFID cards. However, these challenges were quickly resolved by adjusting and improving the device’s functions. Minor tweaks are part of any project, Ville laughs.
Internal challenges included team changes, but these were addressed by thoroughly onboarding new members and ensuring smooth communication.
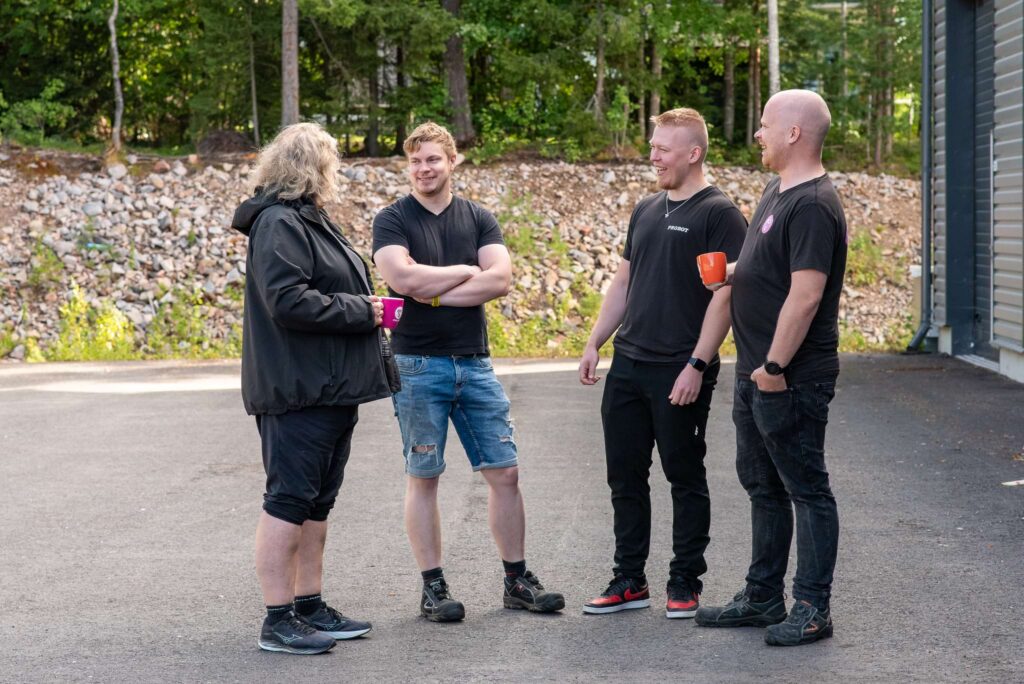
The resulting robotic cell met the project’s goals. The success was due to the project team’s seamless collaboration and quick response to challenges.
– Our client has been extremely satisfied with the outcome and has given positive feedback on the team’s professionalism, flexible approach, and positive attitude. The project progressed according to plan, and the client felt that their needs were considered at every stage, Juha says with a smile.
The entire team thanks the client for the smooth communication and flexible cooperation.
– Working with the client went smoothly in every way.
“Robotics brings efficiency, precision, and flexibility to production, which is essential for maintaining competitiveness.”
Customizable Material Handling Cell Suited for Multiple Industries
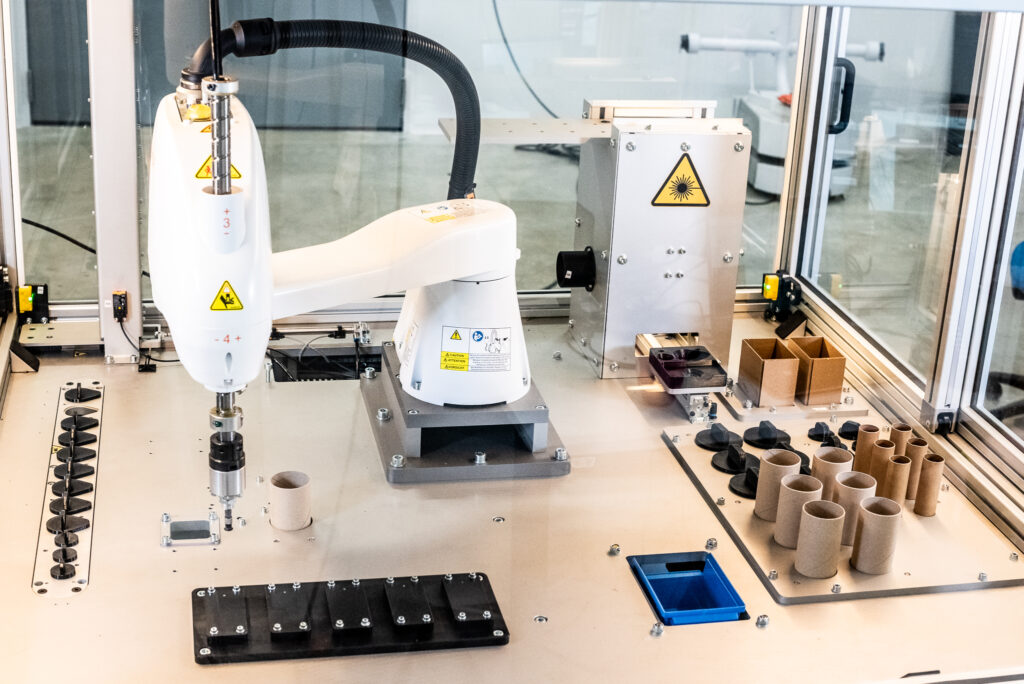
This project provided the Probot team with valuable experience and the opportunity to further develop our expertise and create a new concept that we can utilize in the future. The versatile material handling cell we designed for RFID tag handling is suitable for multiple industries. Its modular structure and programmability make it a flexible solution for various production processes, such as assembly, quality control, and packaging.
The versatility and scalability of this solution allow it to be adapted for different applications through further development, making the cell ideal for future needs. Its compact size means the robotic cell takes up very little floor space and can be easily relocated if production needs change. Additionally, the cell can be customized in size and functionality to match space and operational requirements. The ability to use a wide range of robots further enhances the customization options to meet the specific needs of different industries.
If you’re considering acquiring a robotic cell for your production, here are a few tips:
– Ensure that product specifications are clearly defined before starting the project to avoid surprises during implementation, Ville advises.
To ensure a successful project, the Probot team emphasizes the importance of thorough documentation, effective communication throughout the project, and selecting the right technologies and methods. It’s also crucial that the team is well-prepared and thoroughly briefed on the project’s requirements.
Robotics Can Enhance Production Competitiveness
The project team unanimously agrees that the role of robotics in domestic industry is significant and is expected to grow in the future. The team also believes that robotics will create new job opportunities.
– Robotics brings efficiency, precision, and flexibility to production, which is essential for maintaining competitiveness. It will be a central part of industrial development and will help companies respond quickly to changing market demands. We believe that the use of robotics will continue to expand in the future, Toni predicts.
The benefits of robotics open up new possibilities for industrial development and enhance production competitiveness.
Interested? Feel free to contact us, and together we’ll explore how we can help you take advantage of robotics in your production!
Read More:
- Learn more about the RFID tag handling cell in our references here.
- Also, check out our blog about the palletizing robotic cell here.
Probot Oy – Specialist in Robotics.