Tommi Pekkala, CEO of Pattijoen Kalustetekniikka and packer Satu Sorola urge to give up unnecessary prejudices and approach the technology brought by robots with curiosity. According to them, robot is the most excellent production aid, which can be allowed to handle the most monotonous and heavy jobs of the line. The well-being and occupational safety of the working community improve at the same time as production becomes more efficient.
Pattijoen Kalustetekniikka Oy, which manufactures kitchen furniture components, is a family business founded in 1990. The company, located near Raahe in Pattijoki, once manufactured kitchens for houses but has since completely switched over to manufacturing components.
-We manufacture high-quality, fully mechanized, ready-to-assemble frame and furniture components for kitchen, closet, and toilet furniture. Our customers are, for example, fixed furniture manufacturers, installation contractors, and wholesalers, Tommi Pekkala, CEO of Pattijoen Kalustetekniikka Oy says.
-We are a reliable partner. Our operating philosophy is that what we promise, we keep. Above all, we invest in delivery reliability, quality, and flexibility.
Ergonomics and Occupational Safety
Pattijoen Kalustetekniikka Oy is experiencing a period of growth: The order backlog has doubled from a few years ago, and today there are customers all over Finland, all the way to Sweden and Estonia. The strong growth in sales led to the idea of making production more efficient. However, that was not the only reason the company started to consider investing in a robotic cell in the packing house. According to Pekkala, employee ergonomics and occupational safety were also important factors.
-In the packing house, the packages are heavy. The heaviest component packages can weigh up to 30 kilograms and often require two people to lift them. It is possible to make work more efficient with a robot. At the same time, workers are safe, when the robot handles the heaviest and most monotonous tasks of the line.
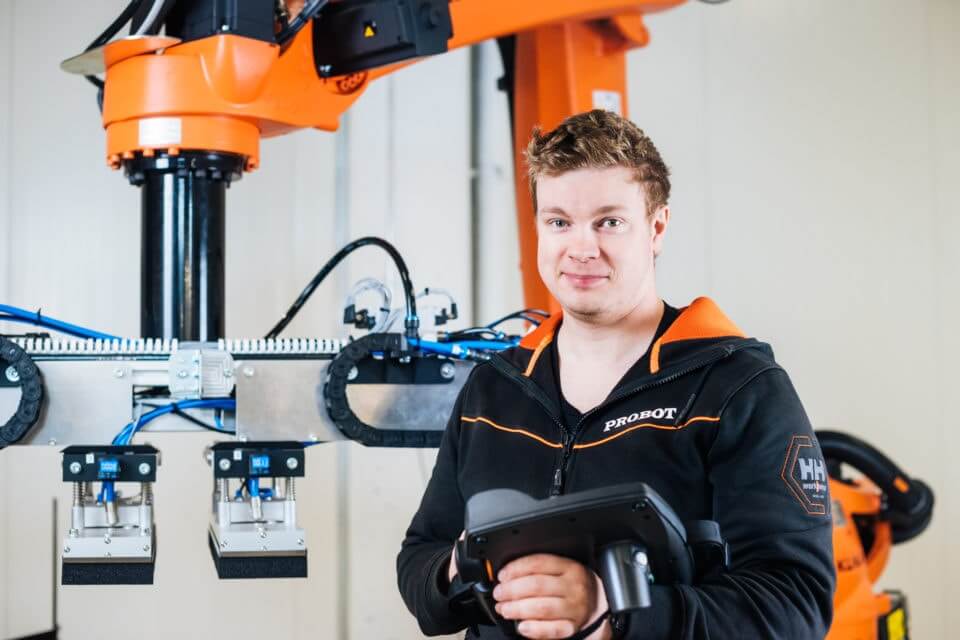
Customized Solutions
Probot Oy designed and implemented a robotic cell for Pattijoen Kalustetekniikka Oy for production use with KUKA’s industrial robot.
-The robot cell was placed at the end of the packaging line to palletize the finished products. In addition to the industrial robot and the conveyor, the cell also includes a barcode scanner and a label printer and gluer, says Toni Autio, Probot Oy’s automation engineer who was responsible for the project.
-We suggested a label printer and gluer for the cell so that the packages already have the required identification labels before they get arranged for transport to the pallets. In this way, the robot can handle the entire work phase independently.
The industrial robot was designed with a gripper tailored to the needs of Pattijoen Kalustetekniikka Oy. The gripper is equipped with foam grippers operating by negative pressure.
-The gripping width of the gripper can be adjusted automatically according to the piece by adjusting the position of the grippers, and either two, three, or four foam grippers can be used as needed. The gripper also has a measuring laser sensor, which allows the robot to measure the actual height of the pallet or stack and place the piece to the right height, design engineer Eetu Koskela explains.
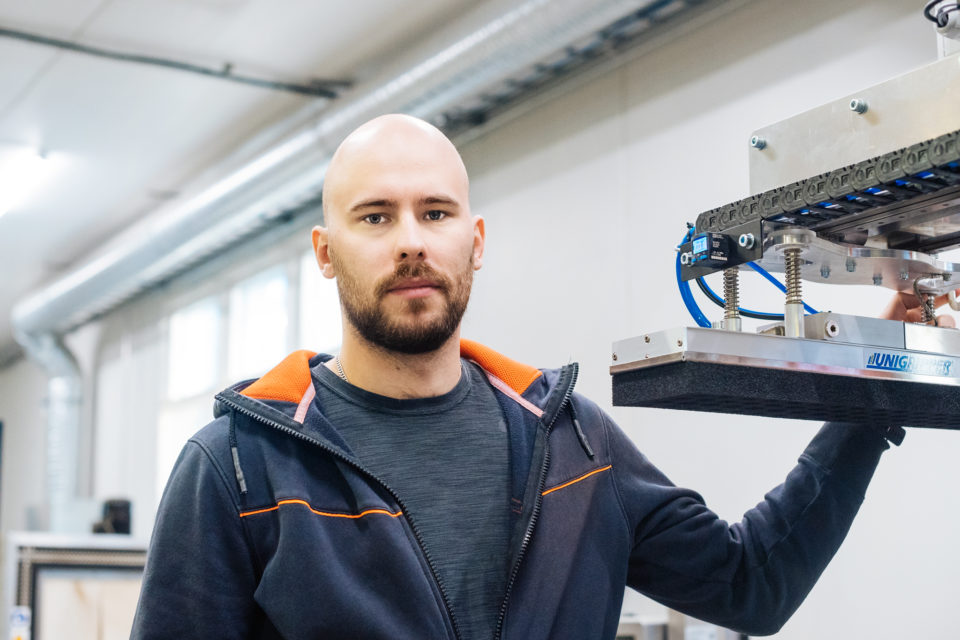
Robot Saves Time and Health
According to Pekkala, the robot-assisted work phase in the packing house is now more than half as faster. In addition, the robot cell improves the ergonomics and occupational safety of employees, as well as the energy efficiency of production.
The employees have also noticed the benefit brought by the robot. Satu Soronen, who works as a packer at Pattijoen Kalustetekniikka Oy, participated in planning the acquisition of the robot cell and is genuinely happy with the result.
-In the packaging department, the work has been continuous. We have tried several times to get the products ready for storage, but they have never made it there. New orders are coming in all the time.
Although the robot cell has only been in use for a short time, according to Soronen, the difference is already noticeable. The robot cell really makes operations more efficient and also saves the workers’ backs.
-You could feel the monotonous lifting of heavy loads in your body. Some days I had to squat for up to eight hours a day. Now that the robot does the heaviest work, your back will thank you.
The Importance of Robotics Increases in the Future
Pattijoen Kalustetekniikka Oy approached Probot Oy regarding the purchase of a robotic cell, because they had previously cooperated with us in the design of a robotic cell. At that time, however, the robot cell was not implemented for practical reasons, but according to Pekkala, we will most likely return to this project in a couple of years. He believes that for Pattijoen Kalustetekniikka Oy, the importance of robotics will increase even more in the future.
-We may not make such large line solutions anymore, but smaller robot cells certainly have their place in production.
According to Pekkala and Soronen, the cooperation with Probot Oy went well, and it was easy to agree on the chosen solutions.
-I was looking forward to the robot cell, and everything seems good. I am constantly learning new things about using the robot. I’ve been very satisfied, says Soronen.
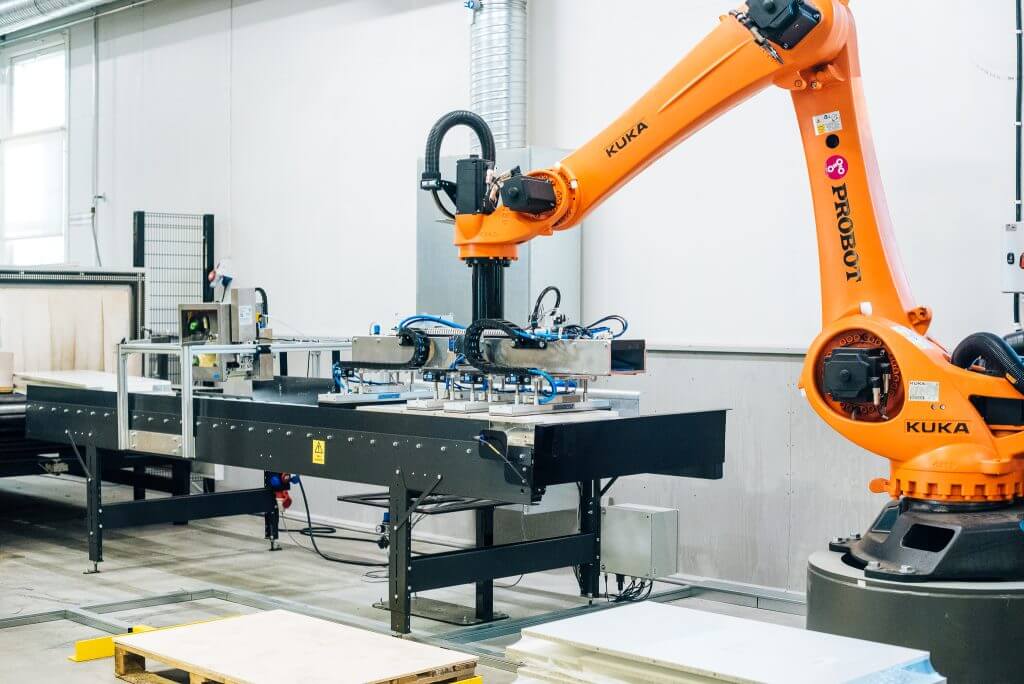
“It’s Good that the Company is Developing”
The robot cell in Pattijoen Kalustetekniikka Oy’s packing house has brought a lot of positive things with it.
-For me, it has brought more knowledge and skills. It’s good that the company is developing all the time. In addition, we have made other reforms thanks to the contribution of the robot. We got a new computer in the packing house, and we have rearranged the shelf and storage places to make the whole packing house more functional. These are small things, but they can make the operation much more efficient. It’s nice that I’ve been able to take part in the operations development myself, Soronen thanks.
-Furthermore, thanks to the robot, much neater component piles leave the packaging house. Corner protectors are now much easier to install when the stacks are straight. After all, it is nice to send such neat and even stacks to the customer.
Above All, a Robot is a Tool for Employees.
Tommi Pekkala thinks that if it is possible to carry out a work step that is difficult or monotonous for humans, it should be carried out with a robot.
-If a company is considering the purchase of a robotic cell, there is no point in delaying it. A robot can help a lot. After finding a suitable partner, it is worth bringing up what kind of work the robot is needed for as comprehensively and thoroughly as possible.
-You shouldn’t be prejudiced. The robot is, above all, a tool for employees, and it is not taking away anyone’s job. People will still have lots of other things to do. Even a robot can’t do everything, Soronen advises.
For those considering a robotic cell, Pekkala also reminds it may be possible to receive a development grant from the ELY Center for the purchase.
-In investments of this size, the grant can help a lot.
Probot Oy – Specialist in Robotics.