Challenges can be painful at times, but above all they help you overcome yourself. This also happened in the year-long MIMIC project. In this EU project implemented under the RIMA project, we used virtual reality and robotics to perform industrial inspection and maintenance tasks. Our XR developer Olli-Pekka Nikka, who reached to great results, says that thanks to MIMIC he learned a lot more about virtual reality development and its current limitations.
The MIMIC (ReMote Inspection and Maintenance activities using MAGOS Platform) implemented under the RIMA project was done in cooperation with the Greek haptic glove developer MAGOS. The cooperation, that started in the EDISON project continued with the new project shortly after the previous one ended. We also cooperated with the University of Oulu’s biomimetics and intelligent systems research group BISG.
Our role in the project was to implement the user interface for the remote control of the robot through virtual reality. The robot operates in the factory environment in areas that are dangerous for people.
From Application Architecture to Development Work
The project was started by mapping the necessary technologies and drawing the so-called architecture from them. Software architecture describes how applications work with middleware and databases.
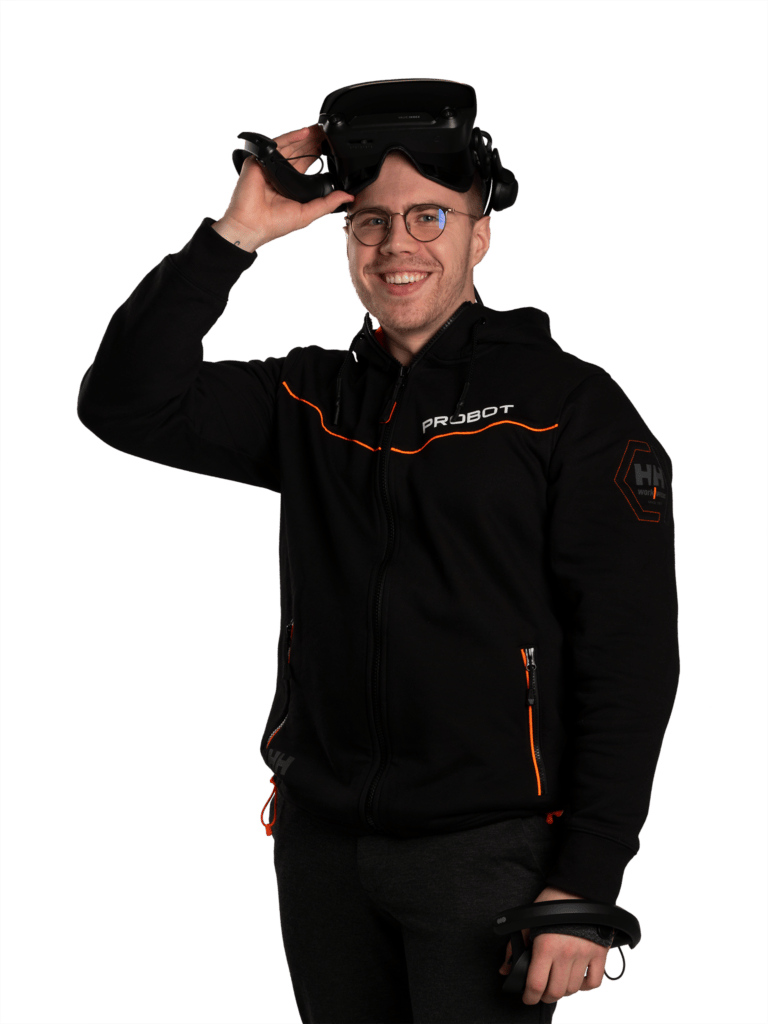
– At first, I looked at how to get all the applications i.e. the necessary pieces, to communicate with each other. When the communication architecture was ready, I started planning the environment and functionalities. When creating functionalities, I had to think about, for example, how to control the robot via virtual reality. I implemented the virtual reality environment with 3D modeling software Blender, using the dimensions of the physical testing space, Olli-Pekka tells.
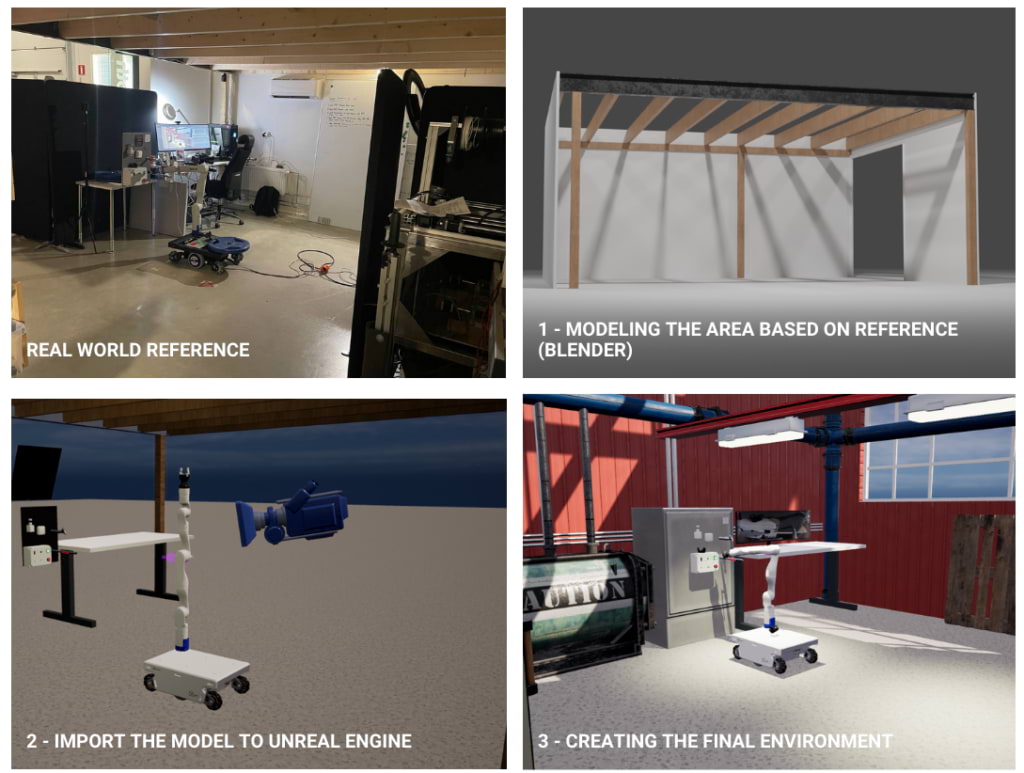
Functioning Results
In this project, the testing phase was only towards the end, because of the availability of the mobile robot, robotic arm, and haptic gloves were limited. So, I did theory-based programming for a long time.
After Kinova Gen3 robotic arm was installed on Olli-Pekka’s workstation, the development of the digital twin began. After the digital twin was ready, we attached the robotic arm to our Dolly™ mobile robot.
When the MAGOS gloves finally arrived at our office, Olli-Pekka started testing and integrating them into the virtual reality system.
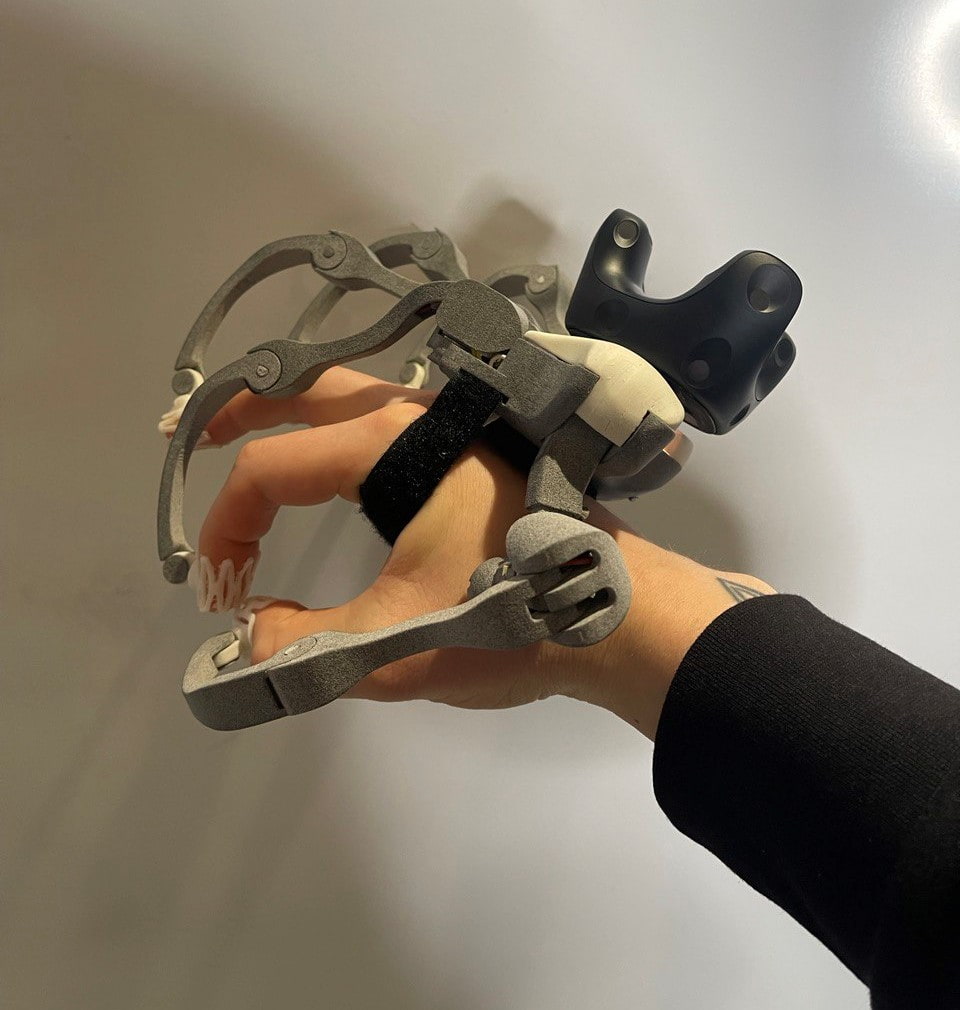
– I developed the operation of the robot arm, haptic gloves, and Dolly™ mostly individually. After the building blocks were developed, I finally started combining their functionalities into a whole.
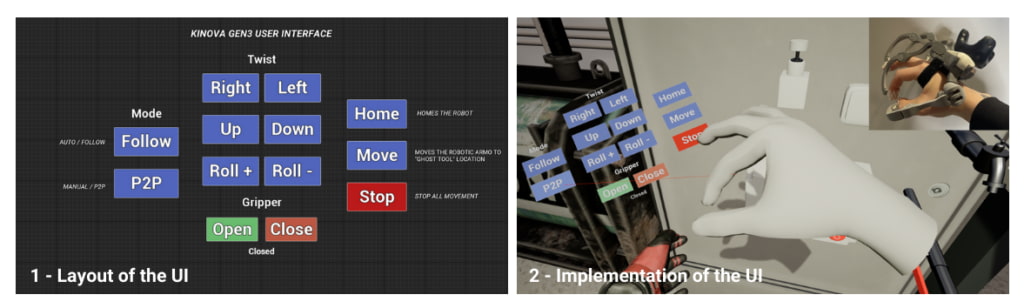
Learning Through Trial and Error
– The most challenging part of the project was the limited availability of resources and time. It was difficult to tackle such a big project alone, and due to the limited hardware availability, I had to rely on my programming skills. During the development phase, I had to restart the project six times, incorporating the knowledge gained from the previous iteration. Therefore, “trial and error” was strongly present.
The most memorable moment in the project was when I got through the very challenging development phase, I got the feeling that I can do this.
Along with the challenges, knowledge and competence accumulate.
– I learned a lot of new things during the project. I learned more in-depth about communication interfaces and protocols. I learned a lot about the XR development with Unreal Engine. I learned about the 3D-modeling with Blender. But most importantly I learned to trust myself and my capability of learning new things.
This was a really challenging project but above all, an interesting and versatile concept. It’s a pleasure to be involved in developing such futuristic technology!
Cooperation with Top Experts
In the hands of skilled and flexible professionals, even a challenging project turns into success. MAGOS founder and CEO Greg Agriopoulos is proud of the project.
– The project was challenging. We set too high expectations at the beginning because we underestimated a few key aspects, for example regarding the hand grip and time management. We had to adapt our goals and strategy during the project. However, being flexible about the original plans paid off, because in the end we managed to successfully complete the project. We are very proud of the result and all the work that we did for it.
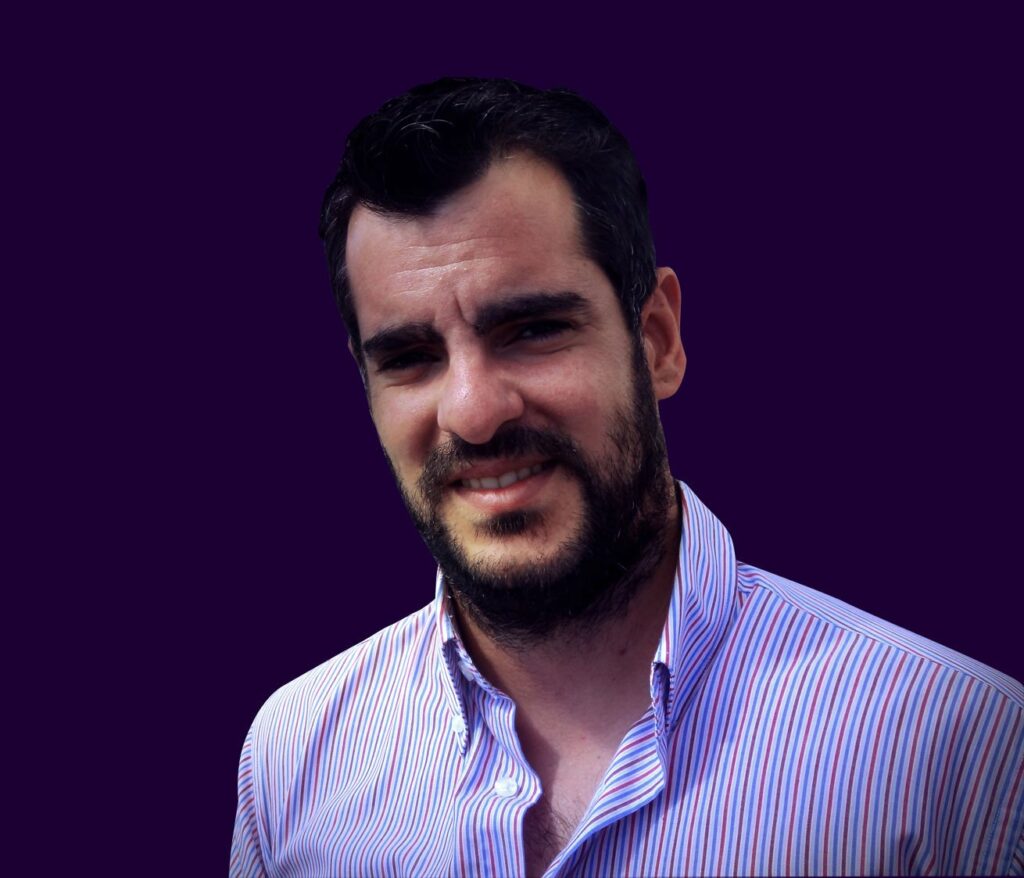
The fluency of the project required active cooperation between the authors. Although the project was implemented remotely from Finland and Greece, the cooperation was smooth.
– Olli-Pekka is a really talented software developer with an excellent ability to develop augmented reality robotics solutions. It is easy to work with him. Olli-Pekka did a lot of work to carry out this project. I believe the project wouldn’t have been completed successfully without him, Greg praises.
Greg sees opportunities to re-commercialize the solution resulting from the MIMIC project on a large scale.
– Our Magos team is strong when it comes to business development. We have already analyzed opportunities and partnerships to commercialize the solution developed in this project. Self-evident alternatives include, for example, performing various inspections and maintenance remotely in various industrial sectors, but we also see many other possibilities. Our team is focused on virtual training and simulation, especially in the aviation and healthcare sectors, as well as in Industry 4.0, i.e. the fourth industrial revolution, which is related to intelligent manufacturing. I see a lot of potential in these application areas with the solution created in the MIMIC project.
I believe that if the MIMIC solution is supplemented with the latest components, it can become a top product on the market.
Cooperation with MAGOS continues in the RIM project funded by Mind for Machines, which started in November. The idea of the project is to make a flexible manufacturing system (FMS), i.e. a production method designed to adapt to changes in the type and quantity of the manufactured product. Machines and computerized systems can be installed to manufacture different parts and handle changing production levels. FMS can therefore improve efficiency and thus reduce the company’s production costs. In addition, it can be a key element in an ordering strategy that allows customers to customize products as they wish.
Probot Oy – Specialist in Robotics.