Mitä jos tuotannon ylijäämämateriaalista voisi tehdä arvokasta resurssia hukkapalan sijaan? Kun asiakkaamme etsi ratkaisua sahausprosessin ylijäämämateriaalin käsittelyyn, lähdimme kehittämään älykästä robottisolua, joka lajittelee materiaalin ja mahdollistaa sen tehokkaan uudelleenkäytön. Ratkaisu osoittautui niin toimivaksi, että investointi maksaa itsensä takaisin jo 2,5 vuodessa. Matkalla tähän tulokseen tarvittiin insinöörihikeä, ratkaisukeskeisyyttä ja oivalluksia.
Jokainen tuotantoprosessi tuottaa jonkin verran hävikkiä, mutta automatisoidulla lajittelulla ja älykkäällä materiaalinhallinnalla tämä hukka voidaan minimoida. Yrityksille tämä ei ole pelkästään ympäristökysymys, vaan myös merkittävä kilpailuetu: kustannussäästöt, resurssien optimointi ja tehokkaampi materiaalin hyödyntäminen parantavat tuotannon kannattavuutta.
Tässä projektissa tavoitteena ei ollut pelkkä lajittelu, vaan solun tuli mahdollistaa ylijäämämateriaalin hyödyntäminen uudelleen ja integroitua saumattomasti asiakkaan tuotantoon. Juuri tällaisiin haasteisiin robotiikka tarjoaa käytännössä toimivia ratkaisuja.
Tämän kaiken toteuttaminen vaatii kuitenkin monialaista osaamista ja saumatonta yhteistyötä. Tässä projektissa Probotin asiantuntijat yhdistivät voimansa kehittääkseen ratkaisun, joka vastaa asiakkaan tarpeisiin tehokkaasti ja luotettavasti.
Luottamus syntyy suosituksista ja asiantuntijuudesta
Kun asiakas päätti investoida robotiikkaan, yhteistyö Probotin kanssa käynnistyi vahvojen suositusten kautta:
– Probot tuli meille puuteollisuuden kontaktien kautta. Suositukset olivat niin vakuuttavia, että lähdimme etenemään juuri heidän kanssaan, asiakas kertoo.
Vaikka uuden teknologian käyttöönottoon liittyy aina epävarmuustekijöitä, valintaa helpotti Probotin kokemus räätälöityjen ratkaisujen toteuttamisesta.
– Missään maailmassa ei ole samanlaista tehdasta kuin meillä. Päätöksentekoa helpotti se, että järjestelmä suunniteltiin täysin meidän tarpeisiin alusta asti. Halusimme ratkaisun, joka ei vaadi suuria muutoksia jälkikäteen, vaan toimii juuri sellaisenaan. Se toi varmuutta investointiin, asiakas summaa.
”Suomen kaltaisissa maissa, jossa palkat nousevat joka vuosi, maailmanlaajuisesta kilpailusta puhumattakaan, yritysten on myös jatkuvasti kehityttävä ja oltava tehokkaita pysyäkseen vauhdissa mukana.”
– Asiakas
Tiimi ongelmanratkaisun ytimessä
Tähän projektiin hyppäsi mukaan joukko Probotin asiantuntijoita. Projektin lankoja käsissään piti projektikoordinaattori Juha Polvela, kun taas mekaniikkasuunnittelusta vastasivat Aleksi Tyni ja Eetu Koskela. Automaatiosuunnittelun puolella Eemeli Mutanen ja Toni Autio tarttuivat teknisiin haasteisiin. Eemeli vastasi lisäksi PLC-ohjelmoinnista ja sähkösuunnittelusta, ja Tonin vastuulla oli automaatiosuunnittelun lisäksi myös robottikoodaus. Kokoonpanovaiheessa myös Jani Juntikka oli mukana tukemassa asennustyötä.
Työ sisälsi hyvin paljon suunnittelua aina konseptoinnista tarkkoihin yksityiskohtiin sekä testauksesta asennukseen ja käyttöönottoon. Projekti kesti kokonaisuudessaan noin 10 kuukautta, ja se sai alkunsa ystävänpäivänä 2024 pidetystä kickoffista.
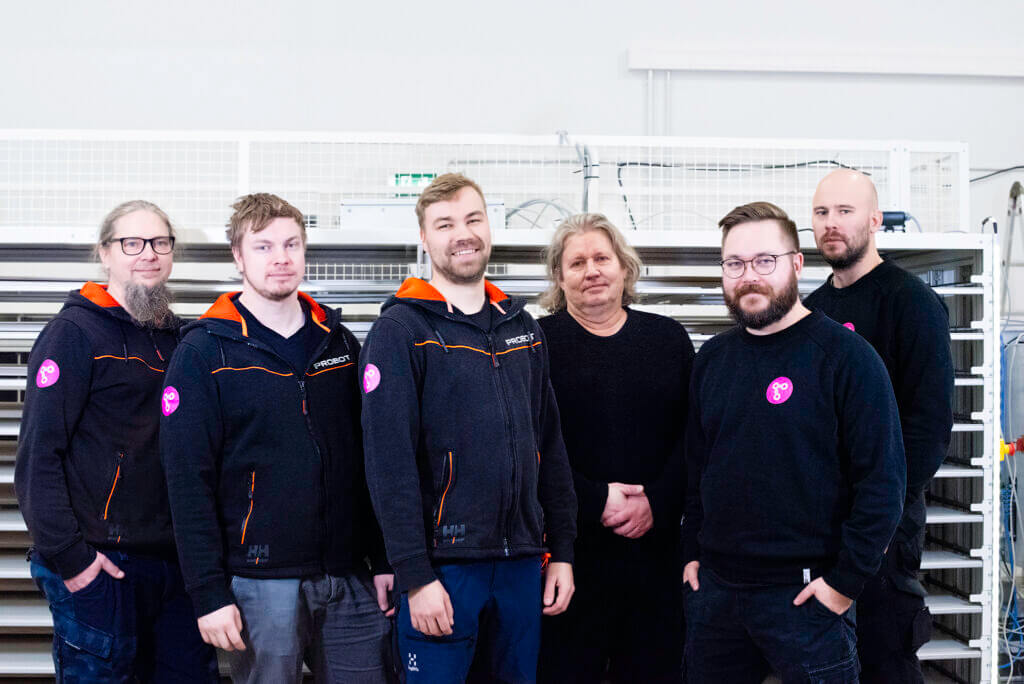
Lyhyesti robottisolun toiminnasta
Tässä ratkaisussa robottisolun toiminta käynnistyy siten, että operaattori asettaa tuotteet tarjottimelle ja syöttää ne soluun.
– Robotti poimii kappaleen, vie sen analysoitavaksi, tarkastaa värin sekä mittaa urasyvyyden ja kaarevuuden, Aleksi kertoo.
– Kun konenäkö on määrittänyt tuotteen kategorian, robotti sijoittaa sen oikeaan lajittelupaikkaan. Jos tuote ei täytä kriteerejä, se menee hylättyjen pinoon.
Tärkeä yksityiskohta oli, että asiakas pystyy hyödyntämään solun poistopuolella hänellä jo muutenkin käytössä olevia vanerilevyjä. Lajitellut tuotteet asetellaan näille levyille hyllyihin eri kategorioiden mukaan.
Solun toiminta kuulostaa yksinkertaiselta, eikö? Todellisuudessa ratkaisun suunnittelu vaati kuitenkin useiden teknisten haasteiden ratkaisemista. Seuraavaksi pureudumme projektin isoimpiin haasteisiin ja siihen, miten ne selätettiin.
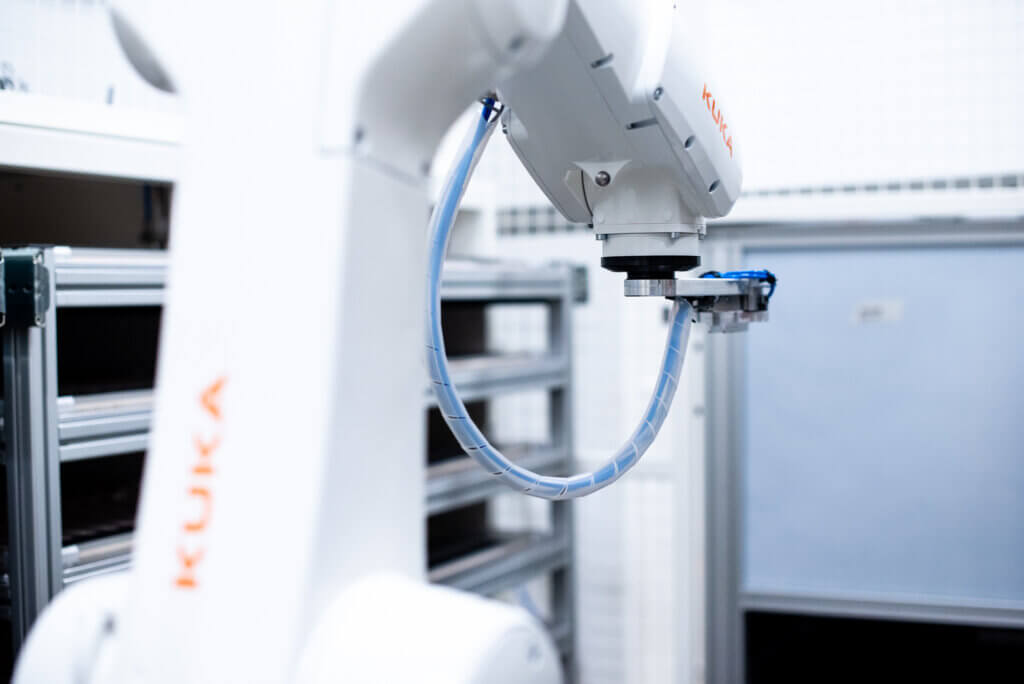
Asiakkaan toiveet haastoivat suunnittelun
Vaikka robottisolu näyttää ulkoisesti vaikuttavalta, suurin työ tehtiin automaation ja koko järjestelmän suunnittelussa. Tiimin täytyi huomioida asiakkaan vaihteleva materiaali, tuotannon tahti sekä turvallisuusratkaisut. Tämä projekti osoitti jälleen kerran, että toimivan automaatioratkaisun kehittäminen vaatii paljon muutakin kuin vain robotin ja tarttujan.
Asiakkaalla oli selkeä näkemys siitä, mitä he halusivat solun tekevän, mutta joitakin vaatimuksia päivitettiin projektin aikana. Ratkaisun suunnittelua ohjasivat muun muassa seuraavat reunaehdot:
➡ Tila määritteli solun maksimikoon ja se täytyi huomioida suunnittelussa alusta asti.
➡ Tahtiaika oli 4 kappaletta minuutissa.
➡ Tuotteita piti pystyä lisäämään ja poistamaan ajon aikana, mikä toi lisähaasteita turvallisuusratkaisuille.
➡ Eri tuotekategorioiden määrä oli suuri, ja solun piti kyetä tunnistamaan ja lajittelemaan kappaleet luotettavasti.
➡ Syöttömekanismin täytyi mahdollistaa 400 tuotteen syöttämisen kerralla.
➡ Materiaalin luonne toi haasteita etenkin syöttöpuolelle. Puu on haastava materiaali, sillä se elää kosteuden mukaan. Tämä korostuu erityisesti ohuissa ja muotoonleikatuissa kappaleissa.
➡ Asiakkaan tuotekappaleet olivat malliltaan uniikkeja, joten niiden käsittelyyn ei ollut valmista ratkaisua. Solu vaati kokonaisvaltaista suunnittelua, jotta kappaleet saatiin käsiteltyä sujuvasti ja luotettavasti.
Turvallisuus ja käytännöllisyys kulkivat tässä projektissa käsi kädessä.
– Koska tuotteita piti voida lisätä ja poistaa solusta lennosta, meidän täytyi miettiä, miten varmistamme turvallisuuden ilman, että tuotanto hidastuu, Aleksi selventää.
”Asiakkaan näkökulmasta tärkeintä on, että ratkaisu toimii. Ja se toimii.”
– Aleksi
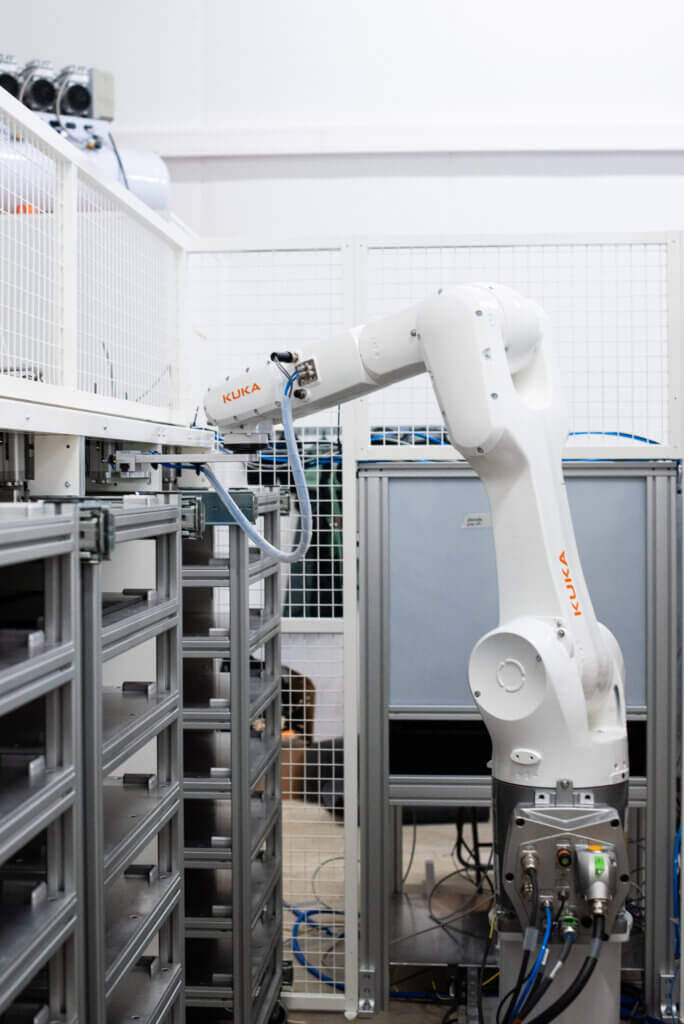
Tekniset haasteet matkalla toimivaan ratkaisuun
Tässä projektissa pari teknistä haastetta nousivat keskeisiksi:
1. Konenäön vaatima tarkka syöttö
Konenäkö ei voi vain ’katsoa’ kappaleita, vaan sen täytyy ymmärtää niiden monimuotoisuus. Tässä solussa konenäkö tunnisti kappaleiden ominaisuudet, joiden perusteella lajittelu tapahtui. Tämä ei kuitenkaan ollut aivan yksinkertaista, sillä asiakkaan uniikkien kappaleiden vaihteleva muoto toi omat haasteensa. Ylijäämäpalat eivät olleet koskaan täysin samanlaisia, joten lajittelun täytyi perustua useisiin eri tekijöihin, kuten kappaleen väriin, urasyvyyteen ja kaarevuuteen.
– Meidän piti varmistaa, että jokainen kappale asettuu juuri oikeaan asentoon analysointia varten. Haaste ei ollut vain kappaleiden poiminnassa, vaan erityisesti siinä, miten ne tuodaan konenäölle niin, että värin, urasyvyyden ja kaarevuuden analysointi onnistuu luotettavasti, Eetu tarkentaa.
Robotti ei voi vain poimia kappaleita satunnaisesti, vaan sen täytyi osata tarttua oikeaan kohtaan ja käsitellä kappaleet luotettavasti. Haasteena ei ollut niinkään itse tarttuminen, vaan se, miten toisistaan poikkeavat kappaleet saatiin asettumaan täsmälleen samaan kohtaan ja asentoon jokaisella syöttökerralla.
2. Solun syöttömekanismin optimointi ja tuotannon tahdin huomioiminen
Solun syöttömekanismi oli toinen kehityskohde, sillä materiaalin syöttö osoittautui odotettua haastavammaksi. Ajatus siitä, että ensimmäinen idea toimii täydellisesti, taitaa olla myytti.
– Alun perin suunniteltu ratkaisu ei pitänyt kappaleita halutussa asennossa, ja jouduimme muokkaamaan syöttöä useaan otteeseen. Automaatiota kehittäessä pitää olla valmis kokeilemaan, hylkäämään ja kehittämään parempia ratkaisuja, Eemeli muistuttaa.
Myös tuotannon tahti piti huomioida. Ratkaisun täytyi mukautua linjan nopeuteen ilman, että se hidasti prosessia.
Virtuaalinen käyttöönotto säästi aikaa
Yksi projektin suurimmista eduista oli virtuaalinen käyttöönotto, jonka ansiosta pääsimme suoraan ajamaan robottia asiakkaan tiloissa heti asennuksen jälkeen.
Loimme robottisolusta todellisuutta vastaavaan mallin KUKA Sim -ympäristössä. Robotti ohjelmoitiin simulaatiossa, ja ohjelmistokoodia testattiin virtuaalisesti ennen fyysistä käyttöönottoa. Näin PLC-koodin ja robottiohjelman synkronointi varmistettiin ennen asennusta, mikä vähensi virheitä. Myös ohjelmistobugit saatiin kiinni jo ennen tehtaalle toimitusta, jolloin käyttöönotto sujui nopeasti.
– Virtuaalinen käyttöönotto oli tässä projektissa iso etu. Pystyimme testaamaan ja varmistamaan kaiken etukäteen, joten paikan päällä ei tullut yllätyksiä, Toni iloitsee.
”Automaatiota voi ottaa käyttöön pienin askelin, aloittaen yksittäisistä pullonkauloista.”
– Aleksi
Sujuvaa yhteistyötä asiakkaan kanssa
Robottisolun asennus vei 3–4 päivää, ja käyttöönotto sujui noin viikossa. Sujuvan käyttöönoton mahdollisti hyvin valmisteltu FAT (Factory Acceptance Test), eli hyväksyntätesti, jossa varmistettiin solun toimivuus ennen toimitusta asiakkaalle. Lisäksi selkeä asennus- ja käyttöönottosuunnitelma sekä saumaton yhteistyö asiakkaan kanssa nopeuttivat prosessia.
– Asennus sujui todella mutkattomasti. Tila oli valmiina, ja saimme tarvittaessa apua asiakkaalta. Hyvä suunnitelma varmisti, että kaikki meni nappiin. Asiakkaan kanssa oli tosi helppo ja miellyttävä toimia, Aleksi kiittelee.
Tiivis kommunikaatio ja selkeä dokumentaatio varmistivat, että ratkaisu vastasi täsmällisesti asiakkaan tarpeita. Asiakas pystyi luottamaan toteutukseen niin vahvasti, että projekti eteni sujuvasti myös ilman jatkuvaa valvontaa.
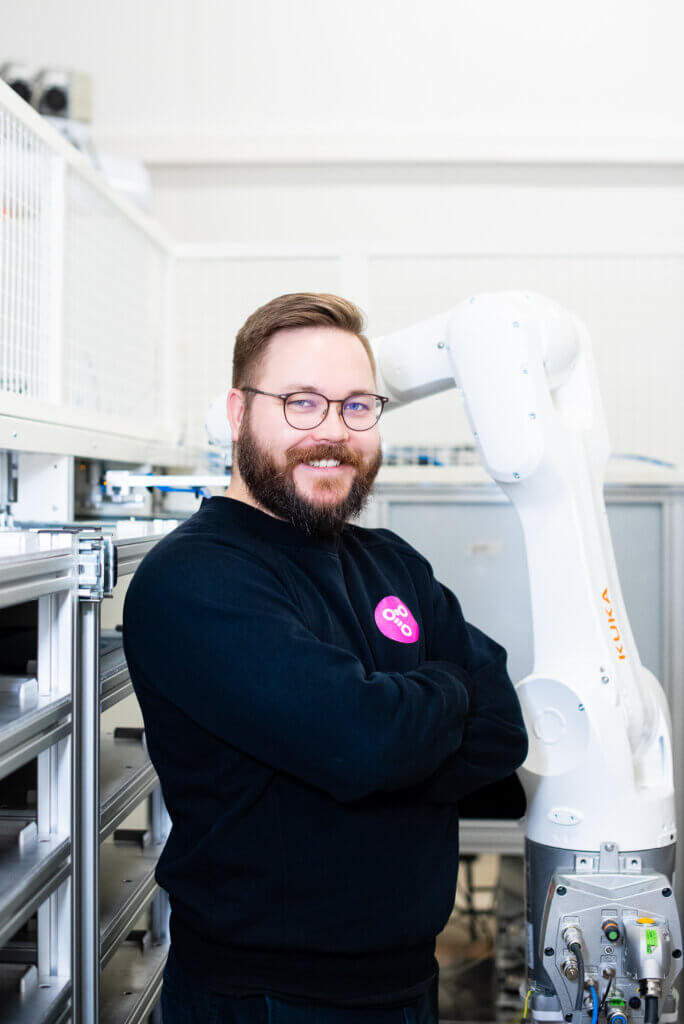
Työntekijät löysivät robotista työkaverin
Automaatioprojekteissa yksi suurimmista haasteista on usein työntekijöiden suhtautuminen uuteen teknologiaan. Epävarmuus ja muutosvastarinta ovat luonnollisia reaktioita, kun tuttuun työympäristöön tuodaan robotti. Näin oli myös tässä projektissa, mutta tilanne muuttui nopeasti, kun työntekijät pääsivät näkemään robottisolun käytännössä.
Alkuvaiheen huolet väistyivät, kun henkilöstö ymmärsi robotin roolin työn tehostajana ja helpottajana. Työnjohto on ollut erityisen tyytyväinen siihen, miten sujuvasti uusi järjestelmä on integroitunut osaksi päivittäistä työtä.
– Alussa oli huhuja siitä, että robotti korvaa työntekijät, mutta kun he pääsivät näkemään sen toiminnassa, ymmärrys lisääntyi. Tämä ei vie työpaikkoja, vaan auttaa meitä tekemään työt paremmin, asiakas kertoo kokemuksistaan.
Miksi automaatioon kannattaa siirtyä nyt?
Robotiikka ja automaatio voivat tuntua suurelta harppaukselta erityisesti niille yrityksille, joilla ei vielä ole niistä kokemusta. Tämä projekti osoitti jälleen kerran, että automaatioon siirtymisen ei tarvitse olla kaikki tai ei mitään. Se voidaan toteuttaa asteittain, liiketoiminnan tarpeisiin sopivalla tavalla.
– Tämä ei ole mikään megatehdas. Tämä on ihan normaalia, järkevää bisnestä, asiakkaamme korostaa ja kannustaa muitakin keskisuuria yrityksiä harkitsemaan automaatiota.
– Uskon, että monet keskikokoiset tuotantolaitokset Suomessa voisivat hyötyä tästä. Vaatii vain uskallusta lähteä mukaan.
Päätös on ollut asiakkaallemme strategisesti tärkeä:
– Suomen kaltaisissa maissa, jossa palkat nousevat joka vuosi, maailmanlaajuisesta kilpailusta puhumattakaan, yritysten on myös jatkuvasti kehityttävä ja oltava tehokkaita pysyäkseen vauhdissa mukana.
Investoinnin kannattavuutta arvioitaessa takaisinmaksuaika on usein keskeinen kysymys:
– Tällä hetkellä arvio on 2,5 vuotta, ja se on jo erittäin hyvä. Kun saamme hyödynnettyä järjestelmää täysimääräisesti, se voi olla vielä lyhyempi.
– Ensimmäisen robottisolun ei tarvitse olla massiivinen. Tärkeintä on löytää sellainen ratkaisu, joka aidosti palvelee tuotantoa ja tekee arjesta helpompaa, Aleksi muistuttaa.
”Automaatioon siirtyminen voi parantaa huomattavasti työntekijöiden turvallisuutta ja ergonomiaa. Se vapauttaa työntekijät mielekkäämpiin tehtäviin monotonisesta, vaarallisesta tai raskaasta työstä.”
– Aleksi
Automaation kolme suurinta hyötyä:
1. Kilpailukyvyn säilyttäminen Suomessa
Automaatio mahdollistaa kustannustehokkaan tuotannon kotimaassa, mikä auttaa pitämään työpaikat Suomessa.
– Robotiikka ja automaatio lisäävät kotimaisten yritysten kilpailukykyä aivan ehdottomasti, Eetu pohtii.
2. Työn mielekkyys sekä turvallisuuden ja ergonomian parantuminen
Robotiikasta ja automaatiosta puhuttaessa ei kannata kuitenkaan keskittyä vain siihen, auttaako tämä ratkaisu tuotannon tehostamisessa.
– Automaatioon siirtyminen voi parantaa huomattavasti työntekijöiden turvallisuutta ja ergonomiaa. Se vapauttaa työntekijät mielekkäämpiin tehtäviin monotonisesta, vaarallisesta tai raskaasta työstä, Aleksi korostaa.
Robotin tarkoitus ei ole korvata ihmistä, eikä viedä kenenkään töitä.
– Tässäkään projektissa robotti ei vienyt kenenkään töitä, vaan päinvastoin toi niitä lisää. Ennen asiakkaan ylijäämämateriaali meni hyödyntämättä roskiin, nyt se saadaan hyötykäyttöön, Eemeli huomauttaa.
3. Asteittainen siirtymä automaatioon ilman massiivista investointia
Aleksi muistuttaa, että automaatiota voi ottaa käyttöön pienin askelin, aloittaen yksittäisistä pullonkauloista.
– On täysin ymmärrettävää, että automaatioon siirtyminen voi tuntua isolta asialta. Mutta on tärkeää huomata, että se ei tarkoita koko tuotannon muuttamista kerralla. Voimme yhdessä suunnitella, mikä olisi järkevin ensimmäinen askel juuri sinun yrityksellesi, Eemeli lisää.
– Tämän projektin jälkeen asiakkaan on nyt paljon helpompi lähestyä robotiikkaa, ja ilmeisesti seuraavat automaatioprojektit ovat jo mielessä, Toni kertoo.
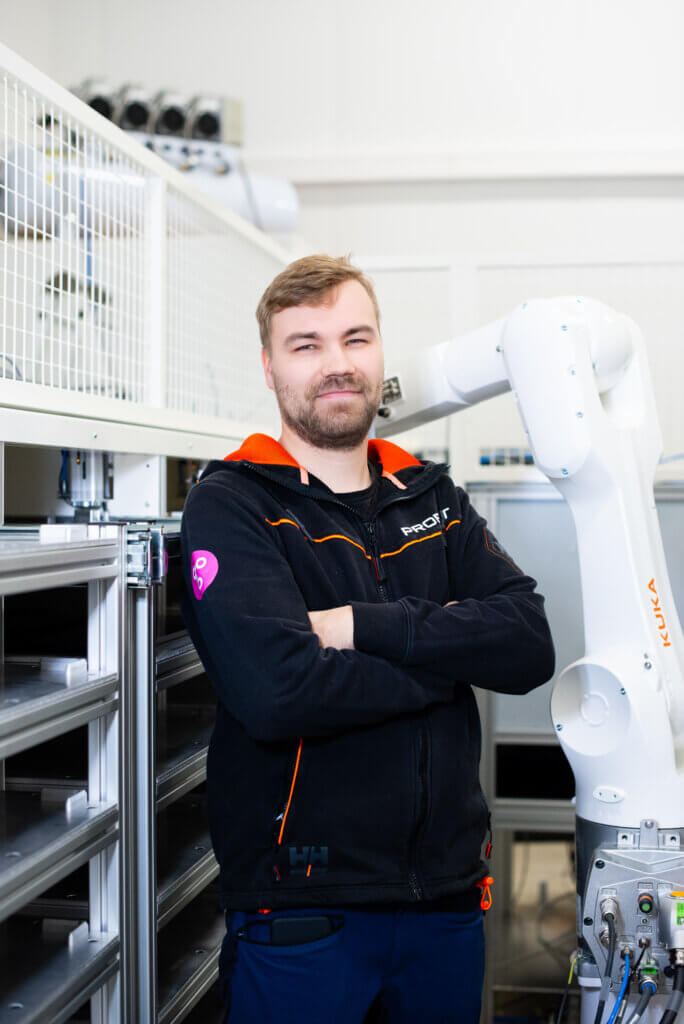
Monipuolinen projekti ja tyytyväinen asiakas
Onnistunut automaatioratkaisu on kokonaisuus, jossa jokainen yksityiskohta tukee toistaan. Asiakas oli erittäin tyytyväinen tarjoamaamme ratkaisuun ja projektiin kokonaisuutena.
– Asiakkaan näkökulmasta tärkeintä on, että ratkaisu toimii. Ja se toimii, tiivistää Aleksi projektin lopputuloksen.
Projekti oli tekijöilleen monipuolinen ja opettavainen. Työhön kuului kaikkea mekaniikkasuunnittelusta ja ohjelmoinnista aina asennukseen ja testaussuunnitteluun.
– Tässä pääsi tekemään niin paljon erilaisia asioita aina suunnittelusta ohjelmointiin ja asennukseen. Työtiimi oli loistava, ja asiakkaan kanssa oli helppo toimia, koko projektitiimi kiittelee.
Uniikki ratkaisu, mutta laajat sovellusmahdollisuudet
Tämä robottisolu on ainoa laatuaan maailmassa. Se on suunniteltu erityisesti puumateriaalin lajitteluun ja käsittelyyn, mutta perusteita voidaan soveltaa muillekin toimialoille.
– Solua muokkaamalla sitä voidaan räätälöidä lähes minkä tahansa tuotteen lajitteluun, Eetu toteaa.
Oli kyseessä sitten hävikin minimointi, laadunvalvonta tai muu tuotannon haaste, avainasemassa on kokonaisvaltainen ymmärrys sekä teknologiasta että asiakkaan prosesseista. Vain näin voimme varmistaa, että automaatio tuo aitoa lisäarvoa, eikä vain teknologian, vaan myös liiketoiminnan näkökulmasta.
Haluatko kuulla lisää siitä, miten automaatio voisi tehostaa yrityksesi tuotantoa?
Ota yhteyttä, niin suunnitellaan yhdessä juuri teille sopiva ratkaisu.
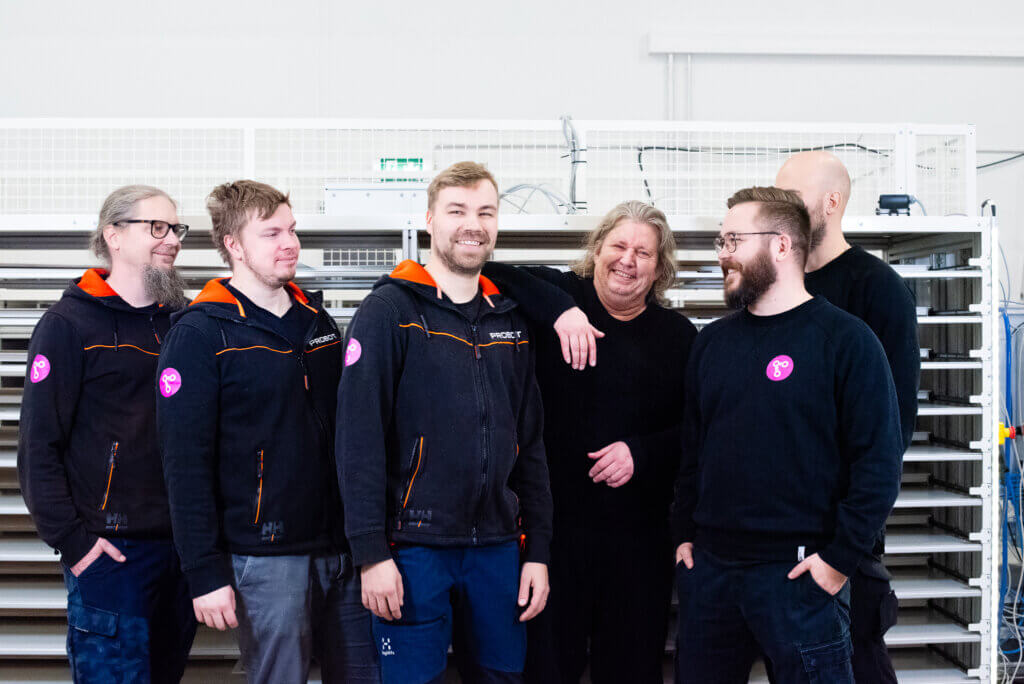
Lue lisää:
- Tutustu tarkemmin tähän projektiin referenssissämme täällä.
- Kiinnostaako RFID-teknologia tai pientuotteiden älykäs käsittely? Lue myös blogimme RFID-tunnisteiden käsittelysolusta täällä.
Probot Oy – Asiantuntijasi robotiikkaratkaisuihin.